Технология заготовительного производства Литые заготовки
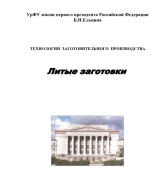
Здравтсвуйте уважаемые посетители сайта Помощь электрикам!
Серийность выпуска деталей - один из главных показателей при
выборе способа производства заготовок. По серийности различают
следующие типы производства: единичное, мелкосерийное, серийное,
крупносерийное и массовое. Для определения типа производства
отливок из черных сплавов можно использовать данные по объему
выпуска деталей и их массе (табл.1).
Специальные способы получения заготовок, требующие более
дорогой и сложной оснастки и специального оборудования, обычно
рентабельны в серийном и массовом производстве. Минимальный размер
партии литых заготовок, для которых целесообразно использование
специальных способов литья, приведен в табл. 2.
Таблица 1
Определение типа производства
Масса
детали,
кг
Годовое число отливок одного наименования, шт.
Производство
единичное мелко-
серийное серийное крупно-
серийное массовое
менее 1 до 700 701-8000 8001-40000 40001-250000 250001
1-8 500 501-6000 6001-30000 30001-200000 200001
8-20 300 301-3000 3001-15000 15001-100000 100001
20-50 200 201-2500 2501-10000 10001-60000 60001
50-100 150 151-2000 2001-8700 8701-53000 53001
100-250 95 96-1400 1401-7000 7001-37500 37501
6
250-500 75 76-1000 1001-4500 4501-25000 25001
500-1000 50 51-600 601-3000 3001-20000 20001
1000-2000 40 41-400 401-2000 2001-13500 13501
2000-5000 20 21-150 151-550 551-4500 ≥4501
Таблица 2
Минимальный размер партии литых заготовок, для которых
целесообразно использование специальных способов литья
Масса
детали,
кг
Способ литья
в
оболочковые
формы
в кокиль,
центробежное
под
давлением
по
выплавляемым
моделям
До 0,063
0,063 – 0,16
0,16 – 0,25
0,25 – 0,63
0,63 – 1,0
1,0 – 1,6
1,6 – 2,5
2,5 – 4,0
4,0 – 10,0
280
280
280
140
100
80
65
50
30
1700
1700
1700
900
700
520
415
330
225
26000
16500
12500
9000
7000
5500
4500
3700
2500
30000
20000
16000
12000
9300
7700
6500
5400
4000
Во многих случаях при использовании групповых методов
изготовления заготовок оказывается эффективно применение
специальных способов литья и в мелкосерийном производстве.
Ниже приводится краткая характеристика способов изготовления
литых заготовок в зависимости от типа производства. Более подробные
данные приведены в литературе [1, 2, 4, 6, 10–13, 15–21, 23, 24, 26].
До 80 % всех отливок в настоящее время изготовляется литьем в
песчано-глинистые формы (ПГФ). Литье в песчано-глинистые формы
–универсальный технологический процесс, который применяется в
единичном и мелкосерийном производстве при ручной формовке по
деревянным моделям, при механизированном изготовлении стержней,
машинной формовке по металлическим моделям является экономичным
вариантом изготовления сложных отливок в крупносерийном и массовом
производстве.
Специальные виды литья (СВЛ), как правило, значительно
повышают стоимость отливок, но позволяют повысить точность и
качество поверхностей отливки, уменьшить припуски, снизить объем
механической обработки.
7
Литье в кокиль – способ, применяемый в серийном производстве, а
при использовании специальных многопозиционных машин – в
крупносерийном и массовом производстве. Этим способом эффективно
отливать отливки из цветных сплавов, чугуна и реже стали. При
наличии сложных внутренних полостей применяют песчаные стержни.
Применение литья в кокиль ограничивается из-за неподатливости
металлической формы и, как следствие, затруднения усадки отливок.
Литье под давлением (ЛПД) является наиболее совершенным
методом получения сложных, тонкостенных, точных отливок в
крупносерийном, массовом производстве, главным образом, из цветных
металлов и пластмасс. Возможность армирования отливок из
алюминиевых, цинковых, медных сплавов и пластмасс недефицитными
сталями значительно расширяет возможности и эффективность данного
способа литья. При групповом методе получения заготовок снижаются
затраты на изготовление пресс-форм и способ литья под давлением
становится рентабельным при производстве партий отливок от 3 до 5 тыс.
шт. в зависимости от массы и сложности литья. Применение литья под
давлением ограничивается высокой стоимостью пресс-форм, наличием в
отливках воздушной пористости, а также невозможностью использования
песчаных стержней.
Центробежный способ литья применяется в серийном и массовом
производстве для получения отливок, имеющих в основном форму тел
вращения (трубы, гильзы, втулки). Полые отливки могут
изготавливаться без стержней, что упрощает и удешевляет процесс их
производства.
Литье в оболочковые формы (кронинг – процесс) применяется в
крупносерийном и массовом производстве деталей мелких и средних
размеров и позволяет в 1,5 – 2 раза снизить трудоемкость механической
обработки и уменьшить расход формовочных материалов в литейных
цехах. Оболочковые формы целесообразно использовать для производства
отливок массой до 80 кг. Более крупные отливки получаются с меньшей
точностью размеров из-за коробления оболочек.
Литье по выплавляемым моделям (ЛВМ) эффективно в
крупносерийном производстве. Этим способом можно отливать любые
черные и цветные сплавы, в том числе высокопрочные, жаростойкие
сплавы. Наиболее часто этот способ применяют для изготовления
стальных мелких (до 1,5 кг) и сложных по геометрии деталей с большим
объемом обработки резанием. Рационально также использование данного
способа литья для сложных деталей, собираемых из нескольких
8
механически обработанных частей и соединяемых с помощью пайки,
винтов, сварки.
2.1.2. Вид сплава, размеры, форма и масса детали.
Способ производства заготовок определяют также в
соответствии с видом сплава, размерами, конфигурацией и массой
детали.
При высоких температурах плавления сплава применяется литье в
песчано-глинистые, оболочковые формы и литье по выплавляемым
моделям, так как при повышенных температурах литья резко снижается
стойкость форм. При повышенной усадке сплава не рекомендуется литье
в кокиль, а при склонности сплава к газовой пористости - литье под
давлением.
Ликвация составляющих сплава исключает изготовление заготовок
центробежным способом.
При литье заготовок в песчано-глинистые формы габариты детали
определяют возможность применения машинной формовки в связи с
ограниченными размерами стола формовочных машин. Максимальные
габариты отливок, которые могут изготовляться машинной формовкой:
длина – от 500 до 2500 мм; ширина – от 400 до 2000 мм, высота – от 190 до
800 мм.
В ряде случаев для крупногабаритных изделий в мелкосерийном
производстве целесообразно применение сварно-литых заготовок
(сложные, разветвленные конструкции или при использовании для
отдельных частей деталей дорогих, дефицитных сплавов).
При использовании специальных точных методов литья в
производстве заготовок имеются ограничения по размерам, конфигурации
и массе отливок (табл.3).
Таблица 3
Ограничения по размерам, конфигурации и массе отливок при специальных
способах литья
Характе
-ристика
отливок
Способы литья
под
давлением в кокиль центробеж
ное
в
оболочковые
формы
по выплав-
ляемым
моделям
Габариты,
мм
До 400 мм,
редко до 800
мм
От 50 до 800
мм, длина до
2000 мм
Диаметр до
800 мм,
высота –
500 мм;
трубы
Отливки
небольших
размеров
600х800х250
мм
До 850 мм
9
длинной до
5000 мм
Сложно
сть
конфигура
ции
Тонкостенные
отливки
сложной
конфигурации
с толщиной
стенок 0,8 –
1,5 мм
Отливки
простой
наружной
формы, без
выступающих
частей,
тормозящих
усадку.
Внутренние
полости могут
оформляться
песчаными
стержнями
Простой
конфигурац
ии, формы
тел
вращения с
толщиной
стенок от 6
до 75 мм
Средней
сложности
детали с
простыми
очертаниями
внутренних
полостей,
равномерной
толщиной
стенок 2,5 – 3
мм
Сложной
конфигурации,
тонкостенные
детали с
толщиной
стенки от 1 – 6
мм
Вид
сплава и
масса
отливки,
кг
Цветные
сплавы
(цинковые,
алюминиевые,
магниевые,
медные,
свинцовые),
пластмассы.
Отливки из
цинковых
сплавов от
0,05 до 30 кг,
из
алюминиевых
сплавов от 0,5
до 25 кг
Цветные
сплавы, чугун,
реже сталь.
Чугунные и
стальные
отливки до
1000 кг,
отливки из
сплавов
цветных
металлов до
100 кг
Неликвиру
ющие
цветные
сплавы,
чугун, реже
сталь,
высоколеги
рованные
сплавы.
Отливки до
1000 кг
Чугун, сталь,
медные
сплавы.
Отливки до 30
кг, реже до 80
кг.
Любые сплавы,
в том числе
жаропрочные,
коррозионност
ойкие сплавы.
Отливки от
0,01 до 15 кг,
реже до 180 кг
2.1.3. Требования к точности и шероховатости поверхности
Точность отливки характеризуют степенью ее приближения к
готовой детали. Чем выше точность детали, тем больше переходов
требуется выполнить при механической обработке отливки. Различают
геометрическую и весовую точность отливок.
Геометрическая точность отливок определяется точностью
размеров, формы, расположения поверхностей, шероховатостью и
волнистостью поверхности и зависит от усадки материала, вида размера
(верх, низ, бок), расположения установочных баз, точности оснастки и
способа изготовления.
Геометрическая точность отливок, получаемых в песчано-глинистых
10
формах по деревянным и металлическим моделям, при ручной и
машинной формовке соответствует 14-18 квалитету, шероховатость Rz =
400 -160 мкм.
Специальные способы литья обеспечивают получение более точных
отливок с точностью и шероховатостью, приближенными к готовой
детали, что снижает, а в некоторых случаях исключает механическую
обработку отдельных поверхностей детали. В табл. 4 приведены данные
по точности и шероховатости заготовок, получаемых специальными
способами литья.
Точность и шероховатость поверхности отливок зависит от вида
материала и качества формы. Для отливок из цветных сплавов
принимаются минимальные значения, для стального литья максимальные.
11
Таблица 4
Точность и шероховатость отливок
Способ литья Квалитет
(ГОСТ25347-82)
Параметр шероховатости,
R z , мкм.
В кокиль 13–16 80–20
Центробежное 15–17 180–20
В оболочковые формы 13–16 160–20
По выплавляемым моделям I2–14 20–10
Под давлением 11–14 40–2,5
2.1.4. Учет технико-экономических показателей
Кроме перечисленных факторов при выборе и обосновании
способа литья необходимо учитывать данные о трудоемкости,
себестоимости изготовления заготовок, коэффициентах использования
металла, весовой точности, производительности оборудования,
длительности производственного цикла [1, 2, 5, 6, 10, 13, 28].
2.2. РАЗРАБОТКА ЧЕРТЕЖА ЛИТОЙ ЗАГОТОВКИ
При разработке чертежа литой заготовки особое внимание
следует уделить вопросам экономии металла и снижению его потерь.
Разработка чертежа литой заготовки выполняется по заданному
конструкторскому чертежу в последовательности, описанной ниже.
2.2.1. Определение рационального положения отливки в
форме, установление плоскости разъема формы.
Исходя из выбранного способа литья, определяют положение
отливки в форме, устанавливают плоскость разъема формы.
Наиболее ответственные элементы отливок располагают снизу
или сбоку. Нижние и боковые поверхности при литье получаются
более качественными, а верхние поражаются газовыми раковинами,
засорами и другими дефектами. Если такое расположение нельзя
выполнить из-за конфигурации отливки, то создаются условия, при
которых литейные пороки (усадочные раковины, шлаковые
включения, газовые пузыри) выводятся в выпоры, прибыли, припуски
на механическую обработку в верхней зоне отливки.
Внешние контуры литой детали должны быть расположены таким
образом относительно плоскости разъема, чтобы обеспечить свободное
извлечение модели из формы, исключить отъемные части и по
возможности стержни. Необходимо стремиться к созданию одной
плоскости разъема, при этом используется правило световых теней,
12
согласно которому теневые участки при воображаемом освещении
детали параллельными лучами в направлении, перпендикулярном к
плоскости разъема формы или стержневого ящика, должны
отсутствовать.
Тонкостенные части, особенно крупногабаритных отливок,
рекомендуется расположить в нижних частях формы, по возможности
вертикально или наклонно. Для массивных отливок с большой
величиной усадки (ковкий чугун, сталь) должен соблюдаться
принцип направленного затвердевания, правильность которого
проверяется методом вписанных окружностей: окружность, вписанная
в любое сечение отливки, должна беспрепятственно проходить
(выкатываться) по любым вышележащим сечениям отливки в
направлении кристаллизации.
Внутренние полости и отверстия в литых заготовках получают
с помощью установленных в литейные формы стержней, которые
используются не только в песчано-глинистых разовых формах, но и в
ряде случаев при литье в постоянные формы (кокиль, центробежное
литье и др.). Стержни усложняют форму. Следует таким образом
располагать отливку в форме, чтобы по возможности избегать
применение стержней или оформлять внутренние полости литой
заготовки за счет выступающих частей формы – «болванов». Стержни
должны надежно устанавливаться в форме, иметь достаточную
жесткость и возможность легкого удаления из отливки. Для
укрепления стержня в форме в стенках отливки предусматриваются
технологические отверстия.
2.2.2. Назначение формовочных уклонов
Для облегчения выемки отливки и модели из формы назначаются
минимальные формовочные уклоны. Формовочные уклоны в отливках
величинами допусков не учитываются и, за счет этих уклонов размеры
отливок могут быть увеличены или уменьшены на величину уклонов.
Применение уклонов увеличивает металлоемкость заготовок и
трудоемкость их механической обработки, поэтому величина уклонов
заготовки должна быть оптимальной, по возможности сведена к
одному виду и назначена в соответствии с ГОСТ 3212 – 92 [ 9 ].
Наличие конструктивных уклонов на чертеже детали исключает
необходимость введения формовочных (технологических) уклонов. В
табл.5 приведена величина уклонов при литье заготовок в песчано-
глинистые формы по металлическим моделям. Чем больше усадка
материала, тем больше назначаются уклоны. Формовочные уклоны на
внутренних поверхностях отливок назначаются большими, чем на
13
наружные.
Для технологического процесса литья под давлением внутренние
уклоны не превышают 1°, а при литье по газифицируемым моделям, по
выплавляемым моделям формовочные уклоны на отливаемых
заготовках обычно не устанавливаются.
Таблица 5
Уклоны при литье в песчано-глинистые формы по металлическим моделям
Высота
поверхности,
мм
Поверхность
наружная внутренняя
До 20 1°30' 3°
20 - 50 1° 2°
50 - 100 0°45 ' 1°
100 - 200 0°30' 0°45 '
300 - 500 0°20' 0°30'
500 - 800 0°20' 0°30'
2.2.3. Выбор минимальной толщины стенок отливок,
определение радиусов закруглений.
Минимальная толщина стенок отливок зависит от их расчетной
прочности, жидкотекучести материала, габаритов и способов
изготовления. Минимальная толщина стенок отливок при литье в
песчано-глинистые формы приведена в табл. 6.
Таблица 6
Минимальная толщина стенок отливки (мм) при литье в песчано-
глинистые формы
Материал Наибольший габаритный размер стенки, мм
до 500 500 – 1500 свыше 1500
Чугун 3 – 5 8 – 10 12 – 15
Сталь 5 – 8 10 – 12 15 – 20
Алюминиевые сплавы 3 – 5 5 – 8 –
Минимальную толщину внутренних стенок отливок следует
принимать на 10 – 30 % меньше, чем у наружных стенок. Для
отливок из модифицированного чугуна толщина стенок должна быть
увеличена на 15 – 20 %, а для легированных сталей – на 20 – 30 %.
Минимальные толщины стенок отливок при литье под
давлением приведены в табл. 7, а при литье в оболочковые формы и
по выплавляемым моделям в табл. 8.
14
Таблица 7
Минимальная толщина стенок отливки (мм) при литье под давлением
Материал Площадь поверхности стенки, см 2
ощадь поверхностиетенки, см2
до 25 25 – 225 225 – 400
Алюминиевые
сплавы 1,0 1,25 – 2,0 2,5 – 4
Бронзы 1,5 2,0 – 3,0 3,5 – 5,0
Цинковые
сплавы 0,8 1,0 – 1,5 2,0 – 3,0
Пластмассы
(термопласты) 0,5 – 1,0 1,0 – 1,5 2,0 – 2,5
Таблица 8
Минимальная толщина стенок отливки (мм) при литье по
выплавляемым моделям и в оболочковые формы
Способ
литья
Материал
Сталь Чугун Алюминиев
ые сплавы Бронзы
Цинков
ые
сплавы
по выплавляемым
моделям, с размером
стенки, мм:
25-100
100-400
Св. 400
2,0 1,0-1,5 2,0 2,0 1-1,5
2,5 2,0 2,5 2,5 2,0
4,0 3,5 3,5 3.5 3,0
в оболочковые формы
с размером стенки, мм:
25-100
100-900
2,5-4,0 2,5-3,5 2,5-4,0 3,0 2,0-3,0
4,0-8,0 3,5-5,0 4,0-7,0 3.0-4,0 3.0-4,0
При проектировании литых деталей необходимо избегать
острых углов. Стенки детали сопрягаются плавными радиусами
закруглений и переходов. Наименьшие значения радиусов
закруглений для отливок, отливаемых в песчано-глинистые формы,
определяются из соотношений толщин сопрягаемых стенок отливок.
При равной толщине стенок:
внутренний радиус: r = a / 2,
где, a – толщина стенки отливки, мм.
15
Наружный радиус: R = a + r.
При различных толщина сопрягаемых стенок:
внутренний радиус r = (a+b)/4,
наружный радиус R = r + (a + b) / 2.
Для отливок, отливаемых литьем под давлением и в кокиль,
величины радиусов закруглений могут быть определены из
соотношений:
при равной толщине стенок:
внутренний радиус r = a / 3,
наружный радиус R = a + r ;
при разных толщинах:
внутренний радиус r = (a + b) / 6,
наружный радиус R = r + (a + b) / 2.
Количество разных значений радиусов закруглений, применяемых
в одной отливке, должно быть минимальным и они берутся из ряда
предпочтительных размеров.
2.2.4. Определение минимальных диаметров отливаемых
отверстий, назначение напусков, приливов
Напуски служат для упрощения изготовления отливки и
назначаются взамен элементов, которые не выполняются при литье:
небольшие отверстия, пазы, канавки, уступы, углубления, резьбы.
Приливы назначают для удобства крепления отливки в
приспособлении при механической обработке.
Отверстия в отливках усложняют технологический процесс литья,
особенно если они имеют малый диаметр и большую глубину. При
литье в песчано-глинистые формы отверстия в отливках
высверливаются, если их диаметры не превышают:
в массовом производстве – 20 мм;
серийном – 30 мм;
индивидуальном – 50 мм.
Минимальные диаметры и глубина отливаемых отверстий в
отливках при различных способах литья приведены в табл. 9.
Таблица 9
Минимальные размеры и глубина отливаемых отверстий
Способ
литья
Материал
Сталь Чугун Алюминиев
ые сплавы
Цинковые
сплавы
Медные
сплавы
Пластма
ссы
в кокиль:
d min , мм 20 -40 10-20 8-12 6-8* 10-14 -
16
глубина
отверстия:
глухого
1,5 d min 1,5 d min 2 d min 2 d min 1,5 d min
-
сквозного 2 d min 3 d min 3 d min 3 d min 2 d min -
под давлением:
d min , мм - - 1,5-2 1-1,5 2,5-5 1-3
глубина
отверстия:
глухого
- - 3 d min 3 d min 3 d min 1,2 d min
сквозного - - 4 d min 6 d min 4 d min 2,5 d min
по
выплавляемым
моделям:
d min , мм 3 2,5 2 - 4-7 -
глубина
отверстия:
глухого
- - 1,5 d min - -
-
сквозного 2 d min 2 d min 2 d min - 2 d min -
в оболочковые
формы:
d min , мм 10 8 6 - - -
глубина
отверстия:
глухого
2 d min 3 d min 5 d min - -
-
сквозного 3 d min 4 d min 6 d min - - -
*) набольшие значения диаметров отверстий принимаются для крупных отливок;
**) d min – минимальный диаметр отливаемых отверстий.
2.2.5. Выбор баз для первой операции механической обработки
заготовок, простановка размеров
На первой операции механической обработки используют
необработанные поверхности детали (черновые базы). В качестве
базирующих поверхностей выбирают те, которые имеют наименьший
припуск. Нельзя использовать поверхности с линиями разъёма от форм,
места расположения прибылей, литников. Если не все поверхности
детали обрабатываются, то в качестве черновых баз принимаются
поверхности, не подлежащие механической обработке.
Простановка размеров на заготовках связана с выбором баз и
выполняется с учётом следующих положений:
1. Первоначально определяются исходные поверхности или оси
заготовок, которые могут быть приняты за литейные базы.
Необрабатываемые поверхности заготовки связываются размерами с
черновой (литейной) базой. При этом не рекомендуется простановка
17
размеров цепочкой.
2. Затем выбираются базы механической обработки, которые
связываются по возможности наименьшими размерами с литейными
базами. Литейные базы могут совпадать с базами механической
обработки. Привязывать формы литой заготовки к размерам
механически обрабатываемых поверхностей и наоборот недопустимо.
Правильный выбор базовых поверхностей способствует
получению более точных размеров и сокращению припусков на
мехобработку. Ниже приведены примеры назначения технологических
баз.
2.2.6. Определение мест установки стержней, прибылей
(выпоров) и расположения элементов литниковой системы
Прибыли увеличивают расход металла и применять их нужно
только по необходимости для сплавов с повышенной усадкой (сталь,
высокопрочный чугун), а также для толстостенных, массивных
отливок.
Прибыли обычно устанавливают на верхних частях отливки (в
узлах сочленений, тепловых узлах). В ряде случаев они выполняют
роль выпоров, которые предназначены для вывода газа, воздуха при
заливке формы.
При выборе мест расположения подводящих элементов
литниковых систем необходимо учитывать следующее: при
изготовлении массивных толстостенных деталей из чугуна и стали
небольшой высоты целесообразен подвод металла сверху, а для
тонкостенных отливок сложной конфигурации, особенно из легких
сплавов, предпочтителен подвод металла снизу.
Места установки прибылей и подвода литниковых систем
желательно располагать на обрабатываемых поверхностях, так как это
исключает необходимость их дополнительной обработки и зачистки.
2.2.7. Выполнение резьб на литых заготовках
При разработке чертежа литой заготовки следует рассмотреть
возможность выполнения резьб литьем. Ряд специальных методов
литья (литье под давлением, литье по выплавляемым моделям)
позволяет получать резьбовые поверхности практически без
механической обработки. При этом необходимо учитывать, что
точность резьб не превышает 6-й степени. При литье из черных
металлов витки резьбы получаются неровными, что требует
дополнительной калибровки метчиками, плашками.
18
Отливку заготовок с резьбовыми поверхностями применяют для
неответственных резьбовых соединений с крупным шагом. Наиболее
технологично получение резьбовых поверхностей на деталях,
отливаемых из цветных сплавов и пластмасс способом литья под
давлением [23]. Минимальные размеры резьбовых поверхностей
заготовок, отливаемых литьем под давлением, приведены в табл. 10.
Таблица 10
Минимальные размеры резьбовых поверхностей заготовок, отливаемых литьем
под давлением
Сплав Шаг
резьбы, мм
Диаметр резьбы, мм
наружной внутренней
Цинковый 0,75 5 10
Магниевый 1,0 6 15
Алюминиевый 1,0 8 20
Медный 1,5 10 –
Внутренние резьбы отливать сложнее, чем наружные, из-за
возможности обжатия резьбового знака (стержня) при заливке,
поэтому изготовление внутренних резьб целесообразно из сплавов с
небольшой усадкой (например, цинковых, алюминиевых). По этой
причине внутреннюю резьбу на отливках из медных сплавов не
получают. Резьбы меньшего диаметра, чем указано в таблице и с
мелким шагом, следует нарезать. Максимальную длину отливаемой
резьбы рассчитывают по формуле:
L = К Td 2 tg(α/2) / q
где L – длина резьбы, мм;
К – коэффициент (К = 100 – 160); нижнее значение интервала
коэффициента К применяется для резьб диаметром до 10 мм.
Тd 2 – допуск среднего диаметра резьбы, мм;
q – усадка заливаемого сплава, %;
α – угол профиля резьбы (60 0 для метрической резьбы).
2.2.8. Назначение припусков и допусков на заготовки
Назначение может быть выполнено расчётно-аналитическим
методом или табличным (опытно-статистическим) методом. Первый
19
метод позволяет более точно рассчитать припуски и используется для
заготовок массового и крупносерийного производства.
Припуски и допуски для отливок из черных и цветных металлов
назначают по таблицам ГОСТ Р 53464–2009. Для отливок из
алюминиевых сплавов, получаемых кокильным литьем, учитывают
требования ОСТ 23.4.51–73 [25]. Припуски назначают на сторону, а
допуски на размер заготовки. ГОСТ Р 53464–2009 устанавливает
основные и дополнительные припуски. Основные припуски
определяют в зависимости от допусков размеров и основного ряда
припусков заготовки (18 рядов). В каждом ряду два значения припуска
– меньшее для грубых квалитетов точности, большее для более точных
квалитетов. Значения основных припусков относят к поверхностям,
находящимся при заливке снизу и сбоку. Для верхних поверхностей
используют большие значения припусков близлежащего ряда.
Дополнительный припуск назначается по ГОСТ Р 53464-2009, если
погрешность относительного расположения поверхности (коробление,
смещение по плоскости разъема) больше половины допуска на
соответствующий размер заготовки. Таблицы ГОСТ Р 53464-2009 и
пример определения точности отливки приведен ниже.
2.2.9. Оформление чертежа отливки
Чертеж отливки выполняется в соответствии с требованиями
стандартов ЕСКД [8].
На чертеже литой заготовки указывают:
– марку материала;
– массу;
– плоскость разъема формы
– шероховатость поверхности.
Чертеж отливки должен содержать технические требования, в
которых отмечают:
– точность отливки, например: 8–5–10–8 см. 0,8, ГОСТ Р 53464–2009
(8 – класс размерной точности; 5 – степень коробления; 10 – степень
точности поверхности; 8 – класс точности массы; допуск смещения –
0,8 мм);
– неуказанные литейные радиусы, формовочные уклоны;
– вид термообработки, твердость;
– вид контроля, требования к качеству отливок;
– величину усадки;
– уклоны;
20
– маркировку;
– размеры для справок.
Чертеж отливки выполняется толстыми сплошными линиями, а
чертеж детали изображается тонкими сплошными линиями. На чертеже
отливки дополнительно наносятся следующие данные:
– припуски на механическую обработку сплошной тонкой линией
(рекомендуется красным цветом) с простановкой их числового значения;
– технологические базы, дополнительные опоры и зажимы для первой
операции механической обработки указываются условным обозначением
по ГОСТ 3.1107-83;
– плоскость разъема модели (формы) тонкой линией с обозначением
верха и низа формы;
– стержни со стержневыми знаками условным обозначением
поверхности стержней, а литниковая система, прибыли и выпоры –
тонкой штрихпунктирной линией (ГОСТ 3.1125-88);
– внутренние контуры обрабатываемых поверхностей, отверстия
малого диаметра, пазы, уступы, небольшой высоты, «закрываемые» в
отливке или имеющие технологические напуски, перекрестной
штриховкой.
21
2.3. ТЕХНОЛОГИЧЕСКИЙ ПРОЦЕСС ИЗГОТОВЛЕНИЯ
ЛИТОЙ ЗАГОТОВКИ
2.3.1. Краткое описание технологического процесса
В данном разделе практической работы дается краткое описание
технологического процесса:
– маршрутная схема техпроцесса, анализ его преимуществ и
недостатков, применяемое оборудование, оснастка для производства
заготовок;
– выводы по эффективности выбранной технологии с оценкой
возможности использования малоотходных технологических процессов
и охраны окружающей среды.
2.3.2. Определение коэффициентов весовой точности,
габаритности, коэффициента использования материала.
В практической работе при оценке эффективности выбранного
технологического процесса должны быть отражены следующие
показатели:
1. Коэффициент весовой точности
Коэффициент весовой точности определяется по формуле
К вт = М д / М з ,
где М д – масса детали, кг;
М з – масса заготовки, кг.
Коэффициент весовой точности наиболее полно характеризует
степень приближения формы и размеров готовой детали к форме
заготовки.
Следует стремиться к тому, чтобы коэффициент весовой точности
К вт соответствовал значениям, характерным для соответствующего типа
производства:
крупносерийное производство – К вт = 0,8…0,9;
серийное – К вт = 0,7…0,8;
мелкосерийное – К вт = 0,6…0,7.
22
2. Коэффициент габаритности.
Коэффициент габаритности К гб определяется по формуле:
К гб = V / M ,
где V – объем отливки, дм 3
М – масса отливки, кг.
Чем меньше коэффициент габаритности, тем более технологична
и рациональна конструкция литой детали.
3. Коэффициент использования материала.
Коэффициент использования материала определяется по формуле:
К им = М д / М им ,
где М д – масса детали, кг.
М им – масса исходного металла (норма расхода), кг.
Коэффициент использования материала отражает общий расход
материала на изготовление детали.
2.4. Определение размеров и других параметров отливки
по ГОСТ Р 53464–2009.
2.4.1. Определение параметров точности литой заготовки
1. Допуски размеров, массы и припуски на механическую обработку
заготовок. Основные определения.
ГОСТ Р 53464–2009 «Отливки из металлов и сплавов. Допуски
размеров, массы и припуски на механическую обработку» [5]
распространяется на отливки из черных и цветных металлов и сплавов и
устанавливает допуски размеров, формы, расположения и неровностей
поверхности, допуски массы и припуски на механическую обработку.
В качестве номинального размера отливки принимается сумма
среднего размера детали и общего припуска на обработку. При
определении номинального размера учитывают технологические
напуски, т.е. местное увеличение тела отливки, обусловленное литейной
технологией. Например, формовочные уклоны, непроливаемые
отверстия, сглаживание местных углублений и т. д.
Точность отливки характеризуется классом размерной точности,
степенью коробления, степенью точности поверхностей и классом
точности массы отливки. К обязательному применению подлежат классы
размерной точности и точности массы. На отдельные размеры и
поверхности отливок допускается устанавливать более жесткие нормы,
чем на отливку в целом.
ГОСТ Р 53464–2009 установлено 22 класса размерной точности
23
отливок: с 1-го по 16-й и шесть промежуточных классов (3т, 5т, 7т, 9т,
11т и 12т) повышенной точности по сравнению с соответствующим
размерным классом. Допуски размеров отливок для различных классов
точности приведены в табл.11. Данная таблица, как и другие справочные
данные, приведены в методическом пособии с сокращенным до
2500…10000 мм диапазоном размеров, а также с некоторыми другими
сокращениями.
24
Таблица 11
Классы размерной точности отливок
Технологический
процесс литья
Наибольший
размер отливки,
мм
Тип сплава
цветны
е легкие
нетермо
-
обраба-
тываем
ые
нетермо-
обрабатыв
аемые
черные и
цветные,
термообра
батываемы
е
цветные
легкие
термо-
обрабаты
ваемые
чугуны и
цветные
тугоплав
кие
термо-
обрабаты
ваемые
стали
1 2 3 4 5 6
Литье под давлением
в металлические
формы и по
выжигаемым
моделям с
применением
огнеупорных
материалов с низким
коэффициентом
термического
расширения
До 100
Св.100 до 250
Св.250 до 630
3т – 6
3 – 7т
4 – 7
3 – 7т
4 – 7
5т – 8
4 – 7
5т – 8
5 – 9т
5т – 8
5 – 9т
6 – 9
Литье по
выжигаемым
моделям с
применением
кварцевых
огнеупорных
материалов
До 100
Св.100 до 250
Св.250 до 630
3 – 7
4 – 8
5т – 9т
4 – 8
5т – 9т
5 – 9
5т – 9т
5 – 9
6 – 10
5 – 9
6 – 10
7т – 11т
Литье по
выплавляемым
моделям с
применением
кварцевых
огнеупорных
материалов
До 100
Св.100 до 250
Св.250 до 630
4 – 8
5т – 9т
5 – 9
5т – 9т
5 – 9
6 – 10
5 – 9
6 – 10
7т – 11т
6 – 10
7т – 11т
7 – 11
Литье под низким
давлением и
в кокиль без
песчаных стержней
До 100
Св.100 до 250
Св.250 до 630
Св.630
до 1600
5т – 9т
5 – 9
6 – 10
7т – 11т
5 – 9
6 – 10
7т – 11т
7 – 11
6 – 10
7т – 11т
7 – 11
8 – 12
7т – 11т
7 – 11
8 – 12
9т – 13т
Литье в песчано- До 100 5 – 10 6 – 11т 7т – 11 7 – 12
25
глинистые сырые
формы из низко
влажных (до 2,8%)
высокопрочных
(более 160 кПа или
1,6 кг/см 2 ) смесей.
Св.100 до 250
Св.250 до 630
Св.630
до 1600
6 – 11т
7т – 11
7 – 12
7т – 11
7 – 12
8 – 13т
7 – 12
8 – 13т
9т – 13
8 – 13т
9т – 13
9 – 13
Литье под низким
давлением в кокиль с
песчаными
стержнями. Литье в
облицованный
кокиль. Литье по
газифицируемым
моделям в ПГФ
Литье в формы,
отверждаемые в
контакте с холодной
оснасткой
До 100
Св.100 до 250
Св.250 до 630
Св.630
до 1600
5 – 10
6 – 11т
7т – 11
7 – 12
6 – 11т
7т – 11
7 – 12
8 – 13т
7т – 11
7 – 12
8 – 13т
9т – 13
7 – 12
8 – 13т
9т – 13
9 – 13
Окончание табл. 11.
1 2 3 4 5 6
Литье в песчано-
глинистые сырые
формы из смесей с
влажностью от 2,8
до 3,5% с прочнстью
от 120 до 160 кПа (от
1,2 до 1,6 кг/см 2 ).
Литье центробежное
(внутренние
поверхности). Литье
в формы,
отверждаемые в
контакте с горячей
оснасткой. Литье в
вакуумно-пленочные
песчаные формы
До 100
Св.100 до 250
Св.250 до 630
Св.630
до 1600
Св.1600
до 4000
6 – 11т
7т – 11
7 – 12
8 – 13т
9т – 13
7т – 11
7 – 12
8 – 13т
9т – 13
9 – 13
7 – 12
8 – 13т
9т – 13
9 – 13
10 – 14
8 – 13т
9т – 13
9 – 13
10 – 14
11т – 14
Литье в песчано-
глинистые сырые
формы из смесей с
влажностью от 3,5 до
4,5 % и прочностью
от 60 до 120 кПа (от
0,6 до 1,2 кг/см 2 ).
До 100
Св.100 до 250
Св.250 до 630
Св.630
до 1600
Св.1600
до 4000
7т – 11
7 – 12
8 – 13т
9т – 13
9 – 13
7 – 12
8 – 13т
9т – 13
9 – 13
10 – 14
8 – 13т
9т – 13
9 – 13
10 – 14
11т – 14
9т – 13
9 – 13
10 – 14
11т – 14
11 – 15
26
Литье в оболочковые
формы из
термореактивных
смесей. Литье в
формы,
отверждаемые вне
контакта с оснасткой
без тепловой сушки.
Литье в формы из
жидких
самотвердеющих
смесей. Литье в
песчано-глинистые
подсушенные и сухие
формы
До 100
Св.100 до 250
Св.250 до 630
Св.630
до 1600
Св.1600
до 4000
7 – 12
8 – 13т
9т – 13
9 – 13
10 - 14
8 – 13т
9т – 13
9 – 13
10 – 14
11т - 14
9т – 13
9 – 13
10 – 14
11т – 14
11 - 15
9 – 13
10 – 14
11т – 14
11 – 15
12 - 15
Литье в песчано-
глинистые сырые
формы из
высоковлажных
(более 4,5 %)
низкопрочных (до 60
кПа или 0,6 кг/см 2 )
смесей с низким
уровнем уплотнения
до твердости ниже 70
единиц
До 100
Св.100 до 250
Св.250 до 630
Св.630
до 1600
Св.1600
до 4000
7 – 12
8 – 13т
9т – 13
9 – 13
10 – 14
8 – 13т
9т – 13
9 – 13
10 – 14
11т – 14
9т – 13
9 – 13
10 – 14
11т – 14
11 – 15
9 – 13
10 – 14
11т – 14
11 – 15
12 – 15
В технических требованиях чертежа отливки или детали с
нанесенными размерами отливки должны быть указаны нормы точности
отливки в следующем порядке:
- класс размерной точности;
- степень коробления;
- степень точности поверхностей;
- класс точности массы;
- допуск смещения отливки.
Пример условного обозначения точности отливки 9-го класса
размерной точности, 6-й степени коробления, 15-й степени точности
поверхностей, 9-го класса точности массы с допуском смещения 2,0 мм:
Точность отливки 9-6-15-9 см. 2,0 ГОСТ Р 53464–2009.
Ненормируемые показатели точности отливки заменяют нулями, а
обозначение допуска смещения опускают. Например, точность отливки
9-0-0-9 ГОСТ Р 53464–2009.
2. Определение класса размерной точности отливки
27
Основанием для назначения класса размерной точности отливок
служат следующие исходные данные:
- технологический процесс получения отливки (способ литья);
- тип сплава;
- наибольший габаритный размер отливки;
- тип производства;
- группа сложности отливки.
Диапазон классов размерной точности отливки, обеспечиваемый
различными технологическими процессами изготовления отливок,
приведен в табл. 11 [5, табл. А.1]. В таблице указаны диапазоны
размерной точности отливок, обеспечиваемые различными
технологическими процессами литья. Меньшие их значения относятся к
простым отливкам и условиям массового автоматизированного
производства, большие – к сложным отливкам единичного и
мелкосерийного производства, средние – к отливкам средней сложности
и условиям механизированного серийного производства.
К цветным легкоплавким сплавам отнесены сплавы с температурой
плавления ниже 700º С, к цветным тугоплавким – сплавы с температурой
плавления выше 700º С. К легким отнесены сплавы с плотностью до 3
г/см 3 , к тяжелым – сплавы с плотностью выше 3 г/см 3 .
ГОСТ Р 53464–2009 не определяет критериев отнесения отливки к
соответствующей группе сложности, оставляя решение этого вопроса на
усмотрение разработчика чертежа отливки, сложность которой
возрастает с увеличением числа конструктивных элементов и
усложнением технологии выполнения элементов в отливке.
Например, требуется установить класс размерной точности отливки
корпуса редуктора из серого чугуна, получаемой литьем в песчано-
глинистые сырые формы с влажностью от 2,8 до 3,5 % и прочностью от
120 до 160 кПа. Сложность отливки средняя. Тип производства –
серийное. Наибольший размер отливки – 400 мм. В соответствии с
исходными данными по табл. 2.1 находим диапазон класса размерной
точности отливки 8–13т (8 – 9т – 9 – 10 – 11т – 11 – 12 – 13т). Принимаем
среднее значение – 11т.
3. Определение класса точности массы отливок
Класс точности массы отливок определяют на основании тех же
исходных данных, которые используют при определении класса
размерной точности отливок: технологический процесс литья, тип
сплава, наибольший габаритный размер отливки, тип производства и
28
группа сложности отливки.
Диапазон классов точности массы отливок, обеспечиваемый
различными технологическими процессами изготовления отливок
приведен в табл. 12 [5, табл. Д.1]. Структура таблицы аналогична
структуре табл. 11. Меньшие значения класса точности массы отливок
относятся к простым отливкам и условиям массового
автоматизированного производства, большие – к сложным отливкам
единичного и мелкосерийного производства, средние – к отливкам
средней сложности и условиям механизированного серийного
производства.
Характеристика типов сплавов приведена в предыдущем пункте
учебного пособия.
Величины допусков массы отливок для данного класса точности
массы и для данной номинальной массы отливки можно определить по
ГОСТ Р 53464–2009 [5, табл.4]. За номинальную массу следует
принимать массу отливки с номинальными размерами.
29
Таблица 12
Классы точности массы отливок
Технологический
процесс
литья
Номинальная
масса
отливки,
кг
Тип сплава
цветные
легкие
нетермо
обрабаты
ваемые
сплавы
нетермо
обрабаты
ваемые
черные и
цветные
сплавы и
термооб
рабатыва
емые
цветные
легкие
сплавы
термо-
обраба-
тываемы
е
чугунны
е и
цветные
тугоплав
кие
сплавы
термо-
обраба-
тываемы
е стали
1 2 3 4 5 6
Литье под давлением в
металлические формы и по
выжигаемым моделям с
применением огнеупорных
материалов с низким
коэффициентом
термического расширения
До 1,0 включ.
Св. 1,0 до 10
Св. 10 до 100
1 – 7
2 – 8
3т – 9т
2 – 8
3т – 9т
3 - 9
3т – 9т
3 – 9
4 – 10
3 – 9
4 – 10
5т – 11т
Литье по выжигаемым
моделям с применением
кварцевых огнеупорных
материалов
До 1,0
Св. 1,0 до 10
Св. 10 до 100
2 – 9т
3т – 9
3 – 10
3т – 9
3 – 10
4 – 11т
3 – 10
4 – 11т
5т – 11
4 – 11т
5т – 11
5 – 12
Литье по выплавляемым
моделям с применением
кварцевых огнеупорных
материалов
До 1,0
Св. 1,0 до 10
Св. 10 до 100
3т – 9
3 – 10
4 – 11т
3 – 10
4 – 11т
5т – 11
4 – 11т
5т – 11
5 – 12
5т – 11
5 – 12
6 – 13т
Литье под низким
давлением и в кокиль без
песчаных стержней
До 1,0
Св. 1,0 до 10
Св. 10 до 100
Св.100 до 1000
Св.1000 до 10000
3 – 10
4 – 11т
5т – 11
5 – 12
6 – 13т
4 – 11т
5т – 11
5 – 12
6 – 13т
7т – 13
5т – 11
5 – 12
6 – 13т
7т – 13
7 – 14
5 – 12
6 – 13т
7т – 13
7 – 14
8 – 15
Литье в песчано-глинистые
сырые формы из низко-
влажных (до 2,8 %)
высокопрочных (более 160
кПа или 1,6 кг/см 2 ) смесей
с высоким и однородным
уплотнением до твердости
не ниже 90 единиц. Литье
под низким давлением в
кокиль с песчаными
стержнями. Литье в
облицованный кокиль.
До 1,0
Св. 1,0 до 10
Св. 10 до 100
Св.100 до 1000
Св.1000 до 10000
4 – 11
5т – 12
5 – 13т
6 – 13
7т – 14
5т – 12
5 – 13т
6 – 13
7т – 14
7 – 15
5 – 13т
6 – 13
7т – 14
7 – 15
8 – 16
6 – 13
7т – 14
7 – 15
8 – 15
9т – 16
30
Литье по газифицируемым
моделям в ПГФ. Литье в
формы, отверждаемые в
контакте с холодной
оснасткой
Окончание табл. 12.
1 2 3 4 5 6
Литье в песчано-глинистые
сырые формы из смесей с
влажностью от 2,8 до 3,5 % с
прочностью от 120 до 160
кПа (от 1,2 до 1,6 кг/см 2 ) со
средним уровнем уплотнения
до твердости не ниже 80
единиц. Литье центробежное
(внутренние поверхности).
Литье в формы,
отверждаемые в контакте с
горячей оснасткой.
Литье в оболочковые формы.
Литье в вакуумно-пленочные
песчаные формы
До 1,0
Св. 1,0 до 10
Св. 10 до 100
Св.100 до 1000
Св.1000 до 10000
5т – 12
5 – 13т
6 – 13
7т – 14
7 – 15
5 – 13т
6 – 13
7т – 14
7 – 16
8 – 16
6 – 13
7т – 14
7 – 16
8 – 16
9т – 16
7т – 14
7 – 15
8 – 15
9т – 16
9 – 16
Литье в песчано-глинистые
сырые формы из смесей с
влажностью от 3,5 до 4,5 % и
прочностью от 60 до 120 кПа
(от 0,6 до 1,2 кг/см 2 ). Литье в
оболочковые формы из
термореактивных смесей.
Литье в формы,
отверждаемые вне контакта с
оснасткой без тепловой
сушки. Литье в формы из
жидких самотвердеющих
смесей. Литье в песчано-
глинистые подсушенные и
сухие формы
До 1,0
Св. 1,0 до 10
Св. 10 до 100
Св.100 до 1000
Св.1000
до 10000
5 – 13т
6 – 13
7т – 14
7 – 15
8 – 15
6 – 13
7т – 14
7 – 15
8 – 15
9т – 16
7т – 14
7 – 15
8 – 15
9т – 16
9 – 16
7 – 15
8 – 15
9т – 16
9 – 16
10 – 16
Литье в песчано-глинистые
сырые формы из
высоковлажных (более 4,5 %)
низкопрочных (до 60 кПа или
0,6 кг/см 2 ) смесей с низким
уровнем уплотнения до
твердости 70 единиц
До 1,0
Св. 1,0 до 10
Св. 10 до 100
Св.100 до 1000
Св.1000
до 10000
6 – 13
7т – 14
7 – 15
8 – 16
9т – 16
7т – 14
7 – 15
8 – 15
9т – 16
9 – 16
7 – 15
8 – 15
9т – 16
9 – 16
10 – 16
8 – 15
9т – 16
9 – 16
10 – 16
11т – 16
31
4. Определение степени точности поверхности отливок
ГОСТ Р 53464–2009 определяет степень точности поверхности
отливок как величину неровностей их поверхности (см. [5]). При
нормировании шероховатости поверхности в машиностроении по ГОСТ
2789-73 аналогичным параметром является величина Rz (даже при
использовании самых прецизионных методов литья не удается получить
поверхности с шероховатостью Ra ≤0,63 мкм, поэтому для оценки
качества литых поверхностей применялся высотный параметр Rz).
Аналогичный критерий используется и для оценки степени точности
поверхности отливок, однако точного определения критерия оценки
величины неровностей поверхности отливок в ГОСТе не приведено.
Для оценки величины неровностей поверхности отливок
установлено 22 степени точности поверхности. Численные значения
допусков для различных степеней точности поверхности отливок
приведены в табл. 13 [5, табл.3]. Соответствие между шероховатостью и
степенями точности поверхности отливки представлено в табл. 14 [5,
табл. Г.1].
Таблица 13
Допуск неровностей поверхностей отливки, мм, не более, для
степеней точности поверхностей отливки
Степень
точности
поверхности
отливки
Допуск
неровностей
поверхности
отливки
Степень
точности
поверхности
отливки
Допуск
неровностей
поверхности
отливки
Степень
точности
поверхности
отливки
Допуск
неровностей
поверхности
отливки
1 0,05 9 0,32 17 2,0
2 0,06 10 0,40 18 2,4
3 0,08 11 0,50 19 3,2
4 0,10 12 0,64 20 4,0
5 0,12 13 0,80 21 5,0
6 0,16 14 1,0 22 6,4
7 0,20 15 1,2
8 0,24 16 1,6
Таблица 14
Соответствие между шероховатостью
и степенями точности поверхностей отливок
Параметр
шероховатост
и
поверхности
Значения шероховатости для степеней точности поверхностей отливки
1 2 3 4 5 6 7 8 9 10 11
Ra,мкм,
не более 2,0 2,5 3,2 4,0 5,0 6,3 8,0 10,0 12,5 16,0 20,0
Rz,мкм, – – – – – – – – – – –
32
не более
Параметр
шероховатост
и
поверхности
Значения шероховатости для степеней точности поверхностей отливки
12 13 14 15 16 17 18 19 20 21 22
Ra,мкм,
не более 25,0 32,0 40,0 50,0 63,0 80,0 100 – – – –
Rz,мкм,
не более – – – – – – – 500 630 800 1000
Степень точности поверхности отливок определяется на основании
тех же исходных данных, которые используются при определении класса
размерной точности отливок: технологический процесс литья, тип
сплава, наибольший габаритный размер отливки, тип производства и
группа сложности отливки.
Степени точности поверхностей отливок, обеспечиваемые
различными технологическими процессами изготовления отливок
приведен в табл. 15 [5, табл. В.1].
Таблица 15
Степени точности поверхностей отливки
Технологический процесс
литья
Наибольший
габаритный
размер
отливки,
мм
Тип сплава
Цветн
ые
легкие
нетермо
-обраба
тываем
ые
сплавы
Нетермо-
обрабатыв
аемые
черные и
цветные
сплавы
и термо-
обрабатыв
аемые
цветные
легкие
сплавы
Термо-
обрабат
ываемы
е
чугуны
и
цветны
е
тугопла
вкие
сплавы
Термо-
обраба
тываем
ые
стали
1 2 3 4 5 6
Литье под давлением в
металлические формы
До 100
Св.100 до 250
Св.250 до 630
2 – 6
3 – 7
4 – 8
3 – 7
4 – 8
5 – 9
4 – 8
5 – 9
6 – 10
5 – 9
6 – 10
7 – 11
Литье в керамические
формы, литье по
выжигаемым и
выплавляемым моделям
До 100
Св.100 до 250
Св.250 до 630
3 – 8
4 – 9
5 – 10
4 – 9
5 – 10
6 – 11
5 – 10
6 – 11
7 – 12
6 – 11
7 – 12
8 – 13
Литье под низким
давлением и в кокиль без
песчаных стержней,
До 100
Св.100 до 250
Св.250 до 630
4 – 9
5 – 10
6 – 11
5 – 10
6 – 11
7 – 12
6 – 11
7 – 12
8 – 13
7 – 12
8 – 13
9 – 14
33
центробежное литье в
металлические формы
Литье в оболочковые формы
из термореактивных смесей.
Литье в вакуумно-
пленочные песчаные формы
До 100
Св.100 до 250
Св.250 до 630
6 – 12
7 – 13
8 – 14
7 – 13
8 – 14
9 – 15
8 – 14
9 – 15
10 – 16
9 – 15
10 – 16
11 – 17
Литье в песчано-глинистые
сырые формы из смесей с
влажностью до 2,8 % с
прочностью более 160 кПа
(1,6 кг/см 2 ) с однородным
уплотнением до твердости
не ниже 90 единиц.
. Литье по газифицируемым
моделям в песчаные формы.
Литье в песчаные
отверждаемые, сухие или
подсушенные формы,
окрашенные покрытиями на
водной основе,
нанесенными
пульверизацией или
окунанием. Литье в кокиль с
песчаными стержнями
До 100
Св.100 до 250
Св.250 до 630
Св.630 до 1600
Св.1600
до 4000
7 – 14
8 – 15
9 – 16
10 – 17
11 – 18
8 – 16
9 – 16
10 – 17
11 – 18
12 – 19
9 – 16
10 – 17
11 – 18
12 – 19
13 – 19
10 – 17
11 – 18
12 – 19
13 – 19
14 – 20
Окончание табл. 15.
1 2 3 4 5 6
Литье в песчано-глинистые
сырые формы из смесей с
влажностью от 2,8 до 3,5 %
с прочностью от 120 до 160
кПа (от 1,2 до 1,6 кг/см 2 ) со
средним уровнем
уплотнения до твердости не
ниже 80 единиц. Литье в
песчаные отвержденные,
сухие или подсушенные
формы, окрашенные
покрытиями на водной
основе, нанесенными
кистью или
самовысыхающими
покрытиями, нанесенными
пульверизацией или окунанием.
До 100
Св.100 до 250
Св.250 до 630
Св.630 до 1600
Св.1600
до 4000
Св.4000
до 10000
8 – 15
9 – 16
10 – 17
11 – 18
12 – 19
13 – 19
9 – 16
10 – 17
11 – 18
12 – 19
13 – 19
14 – 20
10 – 17
11 – 18
12 – 19
13 – 19
14 – 20
15 – 20
11 – 18
12 – 19
13 – 19
14 – 20
15 – 20
16 – 21
Литье в песчано-глинистые
сырые формы из смесей с
влажностью от 3,5 до 4,5 %
До 100
Св.100 до 250
Св.250 до 630
9 – 16
10 – 17
11 – 18
10 – 17
11 – 18
12 – 19
11 – 18
12 – 19
13 – 19
12 – 19
13 – 19
14 – 20
34
и прочностью от 60 до 120
кПа (от 0,6 до 1,2 кг/см 2 ) с
уровнем уплотнения до
твердости не ниже 70
единиц.
Литье в песчаные
отвержденные, сухие или
подсушенные формы,
окрашенные
самовысыхающими или
самотвердеющимипокрытия
ми, нанесенными кистью
Литье в оболочковые
формы из термореактивных
смесей. Литье в формы,
отверждаемые вне контакта
с оснасткой без тепловой
сушки.
Литье в формы из жидких
самотвердеющих смесей.
Литье в песчаные
отвержденные сухие или
подсушенные формы
Св.630до1600
Св.1600
до 4000
Св.4000
до 10000
12 – 19
13 – 19
14 – 20
13 – 19
14 – 20
15 – 20
14 – 20
15 – 20
16 – 21
15 – 20
16 – 21
17 – 21
Литье в песчано-глинистые
сырые формы из
высоковлажных (более 4,5
%) низкопрочных (до 60 кПа
или 0,6 кг/см 2 ) смесей с
низким уровнем уплотнения
до твердости ниже 70
единиц
Литье в песчаные
отверждаемые, сухие или
подсушенные
неокрашенные формы
Литье в формы из жидких
самотвердеющих смесей
До 100
Св.100 до 250
Св.250 до 630
Св.630до1600
Св.1600
до 4000
Св. 4000
до 10000
10 – 17
11 – 18
12 – 19
13 – 19
14 – 20
16 – 20
11 – 18
12 – 19
13 – 19
14 – 20
15 – 20
16 – 21
12 – 19
13 – 19
14 – 20
15 – 20
16 – 21
17 – 21
13 – 19
14 – 20
15 – 20
16 – 21
17 – 21
18 –
22
35
5. Определение допуска смещения отливки по плоскости разъема
Допуск смещения отливки по плоскости разъема определяют по
номинальному размеру наиболее тонкой из стенок отливки, выходящей
на разъем или пересекающих его в соответствии с размерным классом
точности отливки (табл. 18 [5, табл.Б.1]).
6. Определение степени коробления отливки
Степень коробления отливки регламентирует допустимые
погрешности формы и расположения отдельных элементов отливок:
отклонения от прямолинейности, плоскостности, параллельности,
перпендикулярности, заданного профиля и т.д. По ГОСТ Р 53464–2009
установлено 11 степеней точности элементов отливок, значения
допустимых отклонений формы и расположения которых в зависимости
от номинальных размеров данных элементов приведены в табл. 17 [5,
табл. 2]. За номинальный размер нормируемого участка при определении
допусков формы и расположения следует принимать наибольший из
размеров нормируемого участка элемента отливки, для которого
регламентируются отклонения формы и расположения поверхности.
Исходными данными для определения степени коробления отливки
являются:
- отношение наименьшего размера элемента отливки к
наибольшему (толщины или высоты к длине элемента отливки);
- тип формы (разовые или многократные);
- наличие термообработки отливки.
Рекомендуемый диапазон степени коробления отливки представлен
в табл. 18 [5, табл. Б.1]. Меньшие значения из диапазона степеней
коробления относятся к простым отливкам из легких цветных сплавов,
большие значения – к сложным отливкам из черных сплавов.
Степень коробления, указываемую на чертеже отливки, следует
принимать по ее элементу с наибольшей степенью коробления.
36
Таблица 17
Допуски формы и расположения элементов отливки, мм, не более
Номинальный
размер
нормируемого
элемента
отливки, мм
Степени коробления отливки
1 2 3 4 5 6 7 8 9 10 11
До 125 0,12 0,16 0,20 0,24 0,32 0,40 0,50 0,64 0,80 1,00 1,20
Св.125 до 160 0,16 0,20 0,24 0,32 0,40 0,50 0,64 0,80 1,00 1,20 1,60
Св. 160 до 200 0,20 0,24 0,32 0,40 0,50 0,64 0,80 1,00 1,20 1,60 2,00
Св.200 до 250 0,24 0,32 0,40 0,50 0,64 0,80 1,00 1,20 1,60 2,00 2,40
Св.250 до 315 0,32 0,40 0,50 0,64 0,80 1,00 1,20 1,60 2,00 2,40 3,20
Св.315 до 400 0,40 0,50 0,64 0,80 1,00 1,20 1,60 2,00 2,40 3,20 4,00
Св.400 до 500 0,50 0,64 0,80 1,00 1,20 1,60 2,00 2,40 3,20 4,00 5,00
Св.500 до 630 0,64 0,80 1,00 1,20 1,60 2,00 2,40 3,20 4,00 5,00 6,40
Св.630 до 800 0,80 1,00 1,20 1,60 2,00 2,40 3,20 4,00 5,00 6,40 8,00
Св. 800
до 1000
1,00 1,20 1,60 2,00 2,40 3,20 4,00 5,00 6,40 8,00 10,0
Св.1000
до 1200
1,20 1,60 2,00 2,40 3,20 4,00 5,00 6,40 8,00 10,0 12,0
Св. 1200
до 1600
1,60 2,00 2,40 3,20 4,00 5,00 6,40 8,00 10,0 12,0 16,0
Св. 1600
до 2000
2,00 2,40 3,20 4,00 5,00 6,40 8,00 10,0 12,0 16,0 20,0
Св. 2000
до 2500
2,40 3,20 4,00 5,00 6,40 8,00 10,00 12,00 16,00 20,00 24,0
Примечание. За номинальный размер нормируемого участка при определении допусков формы и
расположения следует принимать наибольший из размеров нормируемого участка элемента
отливки, для которого регламентируются отклонения формы и расположения поверхности.
37
Таблица 18
Определение степени коробления элементов отливки
Отношение наименьшего
размера элемента отливки
к наибольшему (толщины
или высоты к длине
элемента отливки)
Многократные формы Разовые формы
Нетермо-
обрабаты-
ваемые
отливки
Термообра-
батываемые
отливки
после
правки
Нетермо-
обрабаты-
ваемые
отливки
Термооб-
рабатываем
ые
отливки
после
правки
Св. 0,200 1 - 4 2 – 5 3 – 6 4 - 7
Св. 0,100 до 0,200 2 – 5 3 – 6 4 - 7 5 - 8
Св.0,050 до 0,100 3 – 6 4 - 7 5 - 8 6 - 9
Св. 0,025 до 0,050 4 - 7 5 - 8 6 - 9 7 - 10
До 0,025 5 - 8 6 - 9 7 - 10 8 - 11
7. Определение допусков размеров отливки
При определении допусков на размеры отливки необходимы следующие
исходные данные:
- класс размерной точности отливки;
- номинальный размер элемента отливки;
- требования к форме и расположению поверхностей отливки.
Допуски размеров элементов отливки в зависимости от класса размерной
точности приведены в таблице 16 [5, табл.1].
Допуски размеров элементов отливки, образованных двумя полуформами или
полуформой и стержнем, устанавливают соответствующими классу размерной
точности отливки. Допуски размеров, образованных одной частью литейной формы
(полуформы) или одним стержнем, устанавливают на 1-2 класса точнее. Допуски
размеров, образованных тремя и более частями литейной формы, несколькими
стержнями или подвижными элементами формы, а также допуски толщины стенок,
образованных двумя и более частями формы или формой и стержнем,
устанавливают на 1-2 класса грубее.
Допуски круглости, соосности, симметричности, пересечения осей,
позиционные допуски в диаметральном выражении не должны
превышать допуски на размеры, установленные в табл.16.
38
Допуски размеров отливок,
Интервал
номинальных
размеров,
мм
Классы размерной
1 2 3т 3 4 5т 5 6 7т
До 4 0,06 0,08 0,10 0,12 0,16 0,20 0,24 0,32 0,40
Св. 4 до 6 0,07 0,09 0,11 0,14 0,18 0,22 0,28 0,36 0,44
Св. 6 до 10 0,08 0,10 0,12 0,16 0,20 0,24 0,32 0,40 0,50
Св. 10 до 16 0,09 0,11 0,14 0,18 0,22 0,28 0,36 0,44 0,56
Св.16 до 25 0,10 0,12 0,16 0,20 0,24 0,32 0,40 0,50 0,64
Св. 25 до 40 0,11 0,14 0,18 0,22 0,28 0,36 0,44 0,56 0,70
Св. 40 до 63 0,12 0,16 0,20 0,24 0,32 0,40 0,50 0,64 0.80
Св. 63 до 100 0,14 0,18 0,22 0,28 0,36 0,44 0,56 0,70 0.90
Св.100 до 160 0,16 0,20 0,24 0,32 0,40 0,50 0,64 0,80 1,00
Св.160 до 250 - - 0,28 0,36 0,44 0,56 0,70 0,90 1,10
Св.250 до 400 - - 0,32 0,40 0,50 0,64 0,80 1,00 1,20
Св.400 до 630 - - - - 0,56 0,70 0,90 1,10 1,40
Св.630 до1000 - - - - - 0,80 1,00 1,20 1,60
Св.1000 до1600 - - - - - - - 1,40 1,80
Св.1600 до 2500 - - - - - - - - 2,00
Св.2500 до 4000 - - - - - - - - -
Св.4000 до 6300 - - - - - - - - -
Св.6300 до10000 - - - - - - - - -
Св.10000 - - - - - - - - -
Для обрабатываемых поверхностей отливок установлено
симметричное расположение полей допусков, для необрабатываемых
поверхностей допускается несимметричное расположение полей
допусков размеров.
2.4.2. Общие принципы назначения припусков
Для обработки заготовок обычно требуется несколько этапов
(последовательных переходов или операций). Припуск на заготовке
необходим для удаления дефектного поверхностного слоя, а также для
компенсации погрешностей формы и взаимного расположения
поверхностей, полученных в результате обработки на предыдущем этапе
или исходной заготовке. Кроме того, необходимо скомпенсировать
погрешность установки заготовки при обработке на данном этапе.
Существует способ определения припуска по таблицам (статистический)
и аналитический (расчетный). При этом минимально необходимый
операционный припуск на сторону Z i min может быть выражен формулой
[3, п. 1.3]
39
Таблица 16
мм, не более
точности
7 8 9т 9 10 11т 11 12 13т 13 14 15 16
0,50 0,64 0,80 1,0 1,2 1,6 2,0 - - - - - -
0,56 0,70 0,90 1,1 1,4 1,8 2,2 2,8 - - - - -
0,64 0,80 1,0 1,2 1,6 2,0 2,4 3,2 4,0 5,0 - - -
0,70 0,90 1,1 1,4 1,8 2,2 2,8 3,6 4,4 5,6 7,0 - -
0,80 1,00 1,2 1,6 2,0 2,4 3,2 4,0 5,0 6,4 8,0 10 12
0,90 1,10 1,4 1,8 2,2 2,8 3,6 4,4 5,6 7,0 9,0 11 14
1,00 1,20 1,6 2,0 2,4 3,2 4.0 5,0 6,4 8,0 10 12 16
1,10 1,40 1,8 2,2 2,8 3,6 4,4 5,6 7,0 9,0 11 14 18
1,20 1,60 2,0 2,4 3,2 4,0 5,0 6,4 8,0 10 12 16 20
1,40 1,80 2,2 2,8 3,6 4,4 5,6 7,0 9,0 11 14 18 22
1,60 2,00 2,4 3,2 4,0 5,0 6,4 8,0 10 12 16 20 24
1,80 2,20 2,8 3,6 4,4 5,6 7,0 9,0 11 14 18 22 28
2,00 2,40 3,2 4,0 5,0 6,4 8,0 10 12 16 20 24 32
2,20 2,80 3,6 4,4 5,6 7,0 9,0 11 14 18 22 28 36
2,40 3,20 4,0 5,0 6,4 8,0 10 12 16 20 24 32 40
3,20 3,60 4,4 5,6 7,0 9,0 11 14 18 22 28 36 44
- - 5,0 6,4 8,0 10 12 16 20 24 32 40 50
- - - 8,0 10 12 16 20 24 32 40 50 64
- - - - 12 16 20 24 32 40 50 64 80
Z i min = Rz (i-1) + h (i-1) + ρ (i-1) + ε i , ( 1 )
где Rz (i-1) – шероховатость поверхности, полученная в результате обра-
ботки на предыдущем этапе;
h (i-1) – глубина дефектного слоя, образованного на предыдущем
этапе обработки;
ρ (i-1) – погрешности формы и расположения поверхности –
результат обработки на предыдущем этапе;
ε i – погрешность установки при обработке на данном этапе.
Индекс i относится к выполняемому переходу, а (i – 1) – к
предшествующему переходу.
Шероховатость поверхности, заданная средним арифметическим
отклонением неровностей профиля Ra , может быть выражена через
параметр Rz по соотношениям:
40
Rz = 4 Ra для диапазона 80 ≤ Ra ≤ 2,5, или:
Rz = 5 Ra для диапазона 2,5 ≤ Ra ≤ 0,01.
При параллельной обработке противоположных поверхностей
суммарный минимальный операционный припуск выражается
формулой:
2 Z i min =2( Rz (i-1) + h (i-1) + ρ (i-1) + ε i ) , ( 2 )
а для поверхностей вращения:
_________
2 Z i min = 2 ( Rz (i-1) + h (i-1) ) +2√ ρ (i-1) 2 + ε i 2 . ( 3 )
Общий припуск на обработку данной поверхности состоит из
суммы промежуточных припусков:
k
Z о = ∑ Z i ,
i-1
где Z о – общий припуск на обработку данной поверхности,
k – количество переходов (этапов), выполняемых при обработке
данной поверхности.
В работе припуски назначаются табличным методом, а расчетным
методом проверяется назначение припуска на одну из рабочих
поверхностей заданной детали.
1. Определение ряда припусков на обработку
Номер ряда припусков на обработку определяет минимальную
величину припуска на поверхности отливки, подлежащей дальнейшей
механической обработке.
Ряд припусков на обработку отливок определяется на основании
следующих исходных данных:
- степени точности поверхности отливок;
- материала отливки;
- типа производства.
Ряды припусков на обработку отливок приведены в табл.19 [5, табл.
Е.1]. Меньшие значения ряда припусков из диапазона их значений
следует принимать для термообрабатываемых отливок из цветных
легкоплавких сплавов, большие значения – для отливок из ковкого
чугуна, средние – для отливок из серого, термообрабатываемых
заготовок из стали и цветных тугоплавких сплавов и высокопрочного
чугуна.
Для поверхностей отливок, располагаемых при заливке вверху,
41
единичного и мелкосерийного производства при изготовлении в
разовых формах допускается применять увеличенные на 1 – 3 единицы
значения ряда припусков.
Таблица 19
Ряды припусков на обработку отливок
Степень
точности
поверхности
1-
2
3-
4
5-
6
7-
8
9-
10
11-
12
13-
14 15 16 17 18 19 20 21 22
Ряды
припусков
1-
2
1-
3
1-
4
2-
5
3-
6 4-7 5-8 6-
9
7-
10
8-
11
9-
12
10-
13
11-
14
12-
15
13-
16
2. Определение общего припуска на сторону
Общий припуск на сторону определяется исходя из следующих
факторов:
- допуск размера детали от базы до обрабатываемой поверхности;
- вид окончательной обработки;
- метод установки отливки при обработке;
- общий допуск элемента поверхности;
- уровень точности обработки;
- ряд припуска;
- тип производства;
- тип обрабатываемой поверхности;
- соотношение между требуемой точностью обработанной
поверхности детали и исходной точностью поверхности отливки.
Минимальный литейный припуск на обработку поверхности
отливки назначают в соответствии с табл. 20 [5, табл. 5] для
поверхностей, обрабатываемых лишь с целью устранения неровностей
и дефектов литой поверхности и уменьшения шероховатости
поверхности при отсутствии необходимости в повышении точности
размеров, формы и расположения обрабатываемых поверхностей.
Таким образом, минимальный литейный припуск компенсирует первые
две составляющие припуска, определяемые аналитически по формулам
(1), (2) и (3) п. 1.
Перед определением общего припуска на обрабатываемую
поверхность необходимо установить соотношение между допусками
размера детали и отливки от базы обработки до обрабатываемой
поверхности (табл. 21 [5, табл. 7]) или между допуском формы и
расположения обработанной поверхности детали и обрабатываемой
42
поверхностью отливки (табл. 22 [5, табл. 8]). В расчет принимают
данные табл. 21 или табл. 22, которые требуют большего уточнения при
обработке исходной заготовки.
Таблица 20
Значения минимального литейного припуска
Ряд
припуска
Минимальный литейный
припуск на сторону, мм,
не более
Ряд
припуска
Минимальный литейный
припуск на сторону, мм, не
более
1 0.1 10 1,6
2 0,2 11 2,0
3 0,3 12 2,5
4 0,4 13 3,0
5 0,5 14 4,0
6 0,6 15 5,6
7 0,8 16 6,0
8 1,0 17 8,0
9 1,2 18 10
Таблица 21
Соотношение между допусками размера детали и отливки и видом
окончательной механической обработки
Допуск размера
отливки,
мм
Соотношение между допусками
размера детали и отливки от базы
обработки до обрабатываемой
поверхности
Вид окончательной
механической
обработки
1 2 3
До 0,5 Св. 0,40
Св. 0,15 до 0,40
Св. 0,10 до 0,15
До 0,10
Черновая
Получистовая
Чистовая
Тонкая
Св. 0,5 до 1,0 Св. 0,30
Св. 0,10 до 0,30
Св. 0,05 до 0,10
До 0,05
Черновая
Получистовая
Чистовая
Тонкая
Св. 1,0 до 2,0 Св. 0,20
Св. 0,10 до 0,20
Св. 0,05 до 0,10
До 0, 05
Черновая
Получистовая
Чистовая
Тонкая
Св. 2,0 до 5,0 Св. 0,15
Св. 0,05 до 0,15
Св. 0,02 до 0,05
До 0, 02
Черновая
Получистовая
Чистовая
Тонкая
43
Св. 5,0 Св. 0,10
Св. 0,05 до 0,10
Св. 0,02 до 0,05
До 0, 02
Черновая
Получистовая
Чистовая
Тонкая
Таблица 22
Соотношение между допуском формы и расположения обработанной
поверхности детали и обрабатываемой поверхности отливки
Допуск размера
отливки, мм
Соотношение между допуском
формы и расположения
обработанной поверхности
детали и допуском
обрабатываемой поверхности
отливки
Вид окончательной
механической обработки
До 0,5 Св. 0,40
Св. 0,10 до 0,40
Св. 0,02 до 0,10
До 0,02
Черновая
Получистовая
Чистовая
Тонкая
Св. 0,5 до 1,0 Св. 0,30
Св. 0,10 до 0,30
Св. 0,02 до 0,10
До 0,02
Черновая
Получистовая
Чистовая
Тонкая
Св. 1,0 до 2,0 Св. 0,20
Св. 0,05 до 0,20
Св. 0,01 до 0,05
До 0, 01
Черновая
Получистовая
Чистовая
Тонкая
Св. 2,0 до 5,0 Св. 0,10
Св. 0,02 до 0,10
Св. 0,005 до 0,02
До 0,005
Черновая
Получистовая
Чистовая
Тонкая
Св. 5,0 Св. 0,05
Св. 0,01 до 0,05
Св. 0,002 до 0,01
До 0,002
Черновая
Получистовая
Чистовая
Тонкая
По соотношению требуемой точности поверхности детали и
точности поверхности исходной заготовки определяют количество
требуемых этапов и вид окончательной механической обработки
44
поверхности. ГОСТ Р 53464-2009 установлено 4 этапа обработки:
черновая, получистовая, чистовая и тонкая. Обычно при механической
обработке литых заготовок четырех этапов достаточно для обеспечения
требуемой точности обрабатываемых деталей, но в ряде случаев
разработанный технологический процесс предусматривает пять и более
последовательных операций, что требует не предусмотренного
стандартом соответствующего увеличения числа межоперационных
припусков и величины общего припуска.
При неуказанных допусках формы и расположения
обрабатываемой поверхности отливки их суммарное значение
принимают равным 25 % допуска размера от базы до обрабатываемой
поверхности отливки.
В случае установки заготовки на станке по установочным базам
без выверки при односторонних отклонениях формы и расположения
обрабатываемой поверхности относительно номинальной, припуск на
размер от установочной базы до обрабатываемой поверхности
назначают с учетом полного значения допуска формы и расположения
обрабатываемой поверхности относительно номинальной. При
установке заготовок в единичном и мелкосерийном производстве с
выверкой по обрабатываемой поверхности припуски назначают с
учетом половинных значений допуска формы и расположения
обрабатываемой поверхности.
Общие припуски на обрабатываемые элементы отливки назначают
по полным значениям общих допусков элементов отливок на размер от
технологической базы до номинального положения обрабатываемой
поверхности детали. Общие допуски элементов отливок в зависимости
от допусков на указанные размеры и допусков формы и расположения
элементов приведены в табл. 23 [5, табл. И.1].
Общие припуски на поверхности вращения и противоположные
поверхности, используемые в качестве взаимных баз при их обработке,
назначают по половинным значениям общих допусков отливки на
соответствующие диаметры или расстояния между противоположными
поверхностями отливки.
В единичном и мелкосерийном производстве при обработке
отливок с установкой отливок с выверкой обрабатываемой поверхности
относительно номинальной поверхности и при односторонних
отклонениях формы и расположения поверхности относительно
номинальной
припуски назначают по половинным значениям допуска формы и
расположения обрабатываемой поверхности. При двухсторонних
45
отклонениях формы и расположения обрабатываемой поверхности
относительно номинальной припуски назначают по полному допуску
формы и расположения.
Значения общего припуска для каждого интервала общих
допусков, расположенных в разных строчках табл. 2.14 [5, табл. 6] и
соответствующие черновой, получистовой, чистовой и тонкой
обработке, выбирают в зависимости от соотношений между требуемой
точностью обработанной поверхностью детали и исходной точностью
поверхности
Таблица 23
Общие допуски элементов отливок, мм
Допуск
размера от
поверхности
до базы
Допуск
формы и
расположения
поверхности
Общий
допуск
элемента
отливки,
не более
Допуск
размера от
поверхности
до базы
Допуск
формы и
расположения
поверхности
Общий
допуск
элемента
отливки,
не более
До 0,01 До 0,01
Св. 0,01 до 0,02
0,02
0,03
Св. 0,06 до 0,08 До 0,02
Св. 0,02 до 0,04
Св. 0,04 до 0,05
Св. 0.05 до 0,06
Св. 0,06 до 0,08
Св. 0,08 до 0,10
Св. 0,10 до 0,12
Св.0,12 до 0,16
0,08
0,09
0,10
0,11
0,14
0,16
0,18
0,22
Св. 0,01 до 0,02 До 0,01
Св. 0,01 до 0,02
Св. 0,02 до 0,03
Св. 0,03 до 0,04
0,02
0,03
0,04
0,05
Св. 0,08 до 0,10
8)
До 0,02
Св. 0,02 до 0,04
Св. 0,04 до 0,06
Св. 0,06 до 0,08
Св. 0,08 до 0,10
Св. 0,10 до 0,12
Св. 0,12 до 0,16
Св. 0,16 до 0,20
0,10
0,11
0,12
0,14
0,16
0,18
0.22
0.28
Св. 0,02 до 0,03
3)
До 0,01
Св. 0,01 до 0,02
Св. 0,02 до 0,03
Св. 0,03 до 0,04
Св. 0,04 до 0,05
Св. 0.05 до 0,06
0,03
0,04
0,05
0,06
0,07
0,08
Св. 0,10 до 0,12
9)
До 0,02
Св. 0,02 до 0,06
Св. 0,06 до 0,08
Св. 0,08 до 0,10
Св. 0,10 до 0,12
Св. 0,12 до 0,16
Св. 0,16 до 0,20
Св. 0,20 до 0,24
0,12
0,14
0,16
0,18
0,20
0,24
0,28
0,32
Св. 0,03 до 0,04
4)
До 0,01
Св. 0,01 до 0,03
Св. 0,03 до 0,04
Св. 0,04 до 0,05
Св. 0.05 до 0,06
Св. 0,06 до 0,08
0,04
0,05
0,06
0,07
0,08
0,11
Св. 0,12 до 0.16
10)
До 0,03
Св. 0.03 до 0,06
Св. 0,06 до 0,10
Св. 0,10 до 0,12
Св. 0,12 до 0,16
Св. 0,16 до 0.20
Св. 0,20 до 0,24
Св. 0,24 до 0,32
0,16
0,18
0,20
0,22
0,28
0,32
0,36
0.44
Св. 0,04 до 0,05
5)
До 0,01
Св. 0,01 до 0,03
Св. 0,03 до 0,04
Св. 0,04 до 0,05
Св. 0.05 до 0,06
Св. 0,06 до 0,08
0,05
0,06
0,07
0,08
0,09
0,11
Св. 0,16 до 0,20
11)
До 0,03
Св. 0,03 до 0,08
Св. 0,08 до 0,12
Св. 0,12 до 0,16
Св. 0,16 до 0,20
Св. 0,20 до 0,24
0,20
0,22
0,24
0,28
0,32
0,36
46
Св. 0,08 до 0,10 0,14 Св. 0,24 до 0,32
Св. 0,32 до 0,40
0,44
0,56
Св. 0,05 до 0.06
6)
До 0,02
Св. 0,02 до 0,03
Св. 0,03 до 0,04
Св. 0,04 до 0,05
Св. 0.05 до 0,06
Св. 0,06 до 0,08
Св. 0,08 до 0,10
Св. 0,10 до 0,12
0,06
0,07
0,08
0,09
0,10
0,12
0,14
0,16
Св. 0,20 до 0,24
12)
До 0,06
Св. 0,06 до 0,12
Св. 0,12 до 0,16
Св. 0,16 до 0,20
Св. 0,20 до 0,24
Св. 0,24 до 0,32
Св. 0,32 до 0,40
Св. 0,40 до 0,48
0,24
0,28
0,32
0,36
0,40
0,50
0,56
0,64
Продолжение табл. 23
Допуск
размера от
поверхности
до базы
Допуск
формы и
расположения
поверхности
Общий
допуск
элемента
отливки,
не более
Допуск
размера от
поверхности
до базы
Допуск
формы и
расположения
поверхности
Общий
допуск
элемента
отливки,
не более
Св. 0,24 до 0,32
13)
До 0,06
Св. 0,06 до 0,12
Св. 0,12 до 0,20
Св. 0,20 до 0,24
Св. 0,24 до 0,32
Св. 0,32 до 0,40
Св. 0,40 до 0,50
Св. 0,50 до 0,64
0,32
0,36
0,40
0,44
0,50
0,56
0,70
0,90
Св. 1,00 до 1,20
19)
До 0,32
Св. 0,32 до 0,64
Св. 0,64 до 0,80
Св. 0,80 до 1,00
Св. 1,00 до 1,20
Св. 1,20 до 1,60
Св. 1,60 до 2,00
Св. 2,00 до 2,40
1,20
1,40
1,60
1,80
2,00
2,40
2,80
3,20
Св. 0,32 до 0,40
14)
До 0,08
Св. 0,08 до 0,16
Св. 0,16 до 0,24
Св. 0,24 до 0,32
Св. 0,32 до 0,40
Св. 0,40 до 0,50
Св. 0,50 до 0,64
Св. 0,64 до 0,80
0,40
0,44
0,50
0,56
0,64
0,70
0,90
1,10
Св. 1,20 до 1,60
20)
до 0,40
Св. 0,40 до 0,80
Св. 0,80 до 1,00
Св. 1,00 до 1,20
Св. 1,20 до 1,60
Св. 1,60 до 2,00
Св. 2,00 до 2,40
Св. 2,40 до 3,20
1,60
1,80
2,00
2,20
2,40
2,80
3,60
4,40
Св. 0,40 до 0,50
15)
До 0,12
Св. 0,12 до 0,24
Св. 0,24 до 0,32
Св. 0,32 до 0,40
Св. 0,40 до 0,50
Св. 0,50 до 0,64
Св. 0,64 до 0,80
Св. 0,80 до 1,00
0,50
0,56
0,64
0,70
0,80
0,90
1,10
1,40
Св. 1,60 до 2,00
21)
До 0,40
Св. 0,40 до 0,80
Св. 0,80 до 1,20
Св. 1,20 до 1,60
Св. 1,60 до 2,00
Св. 2,00 до 2,40
Св. 2,40 до 3,20
Св. 3,20 до 4,00
2,00
2,20
2,40
2,80
3,20
3,60
4,40
5,00
Св. 0,50 до 0,64
16)
До 0,12
Св. 0,12 до 0,24
Св. 0,24 до 0,40
Св. 0,40 до 0,50
Св. 0,50 до 0,64
Св. 0,64 до 0,80
Св. 0,80 до 1,00
Св. 1,00 до 1,20
Св. 1,20 до 1,28
0,64
0,70
0,80
0,90
1,00
1,20
1,40
1,60
1,80
Св. 2,00 до 2,40
22)
До 0,64
Св. 0,64 до 1,20
Св. 1,20 до 1,60
Св. 1,60 до 2,00
Св. 2,00 до 2,40
Св. 2,40 до 3,20
Св. 3,20 до 4,00
Св. 4,00 до 4,80
2,40
2,80
3,20
3,60
4,00
4,40
5,60
6,40
Св. 0,64 до 0,80
17)
До 0,20
Св. 0,20 до 0,40
Св. 0,40 до 0,50
Св. 0,50 до 0,64
0,80
0,90
1,00
1,10
Св. 2,40 до 3,20
23)
До 0,80
Св. 0,80 до 1,60
Св. 1,60 до 2,00
Св. 2,00 до 2,40
3,20
3,60
4,00
4,40
47
Св. 0,64 до 0,80
Св. 0,80 до 1,00
Св. 1,00 до 1,20
Св. 1,20 до 1,60
1,20
1,40
1,80
2,20
Св. 2,40 до 3,20
Св. 3,20 до 4,00
Св. 4,00 до 5,00
Св. 5,00 до 6,40
5,00
5,60
7,00
9,00
Св. 0,80 до 1,00
18)
До 0,24
Св. 0,24 до 0,40
Св. 0,40 до 0,64
Св. 0,64 до 0,80
Св. 0,80 до 1,00
Св. 1,00 до 1,20
Св. 1,20 до 1,60
Св. 1,60 до 2,00
0,80
0,90
1,00
1,10
1,20
1,40
1,80
2,20
Св. 3,20 до 4,00
24)
До 1,00
Св. 1,00 до 1,60
Св. 1,60 до 2,40
Св. 2,40 до 3,20
Св. 3,20 до 4,00
Св. 4,00 до 5,00
Св. 5,00 до 6,40
Св. 6,40 до 8,00
3,20
3,60
4,00
4,40
5,00
5,60
7,00
9,00
Окончание табл. 23
Допуск
размера от
поверхности
до базы
Допуск
формы и
расположения
поверхности
Общий
допуск
элемента
отливки,
не более
Допуск
размера от
поверхности
до базы
Допуск
формы и
расположения
поверхности
Общий
допуск
элемента
отливки,
не более
Св. 4,0 до 5,0
25)
До 1,20
Св. 1,20 до 2,40
Св. 2,40 до 3,20
Св. 3,20 до 4,00
Св. 4,00 до 5,00
Св. 5,00 до 6,40
Св. 6,40 до 8,00
Св. 8,00 до 10,0
5,0
5,6
6,4
7,0
8,0
9,0
11,0
14,0
Св. 16,0 до 20,0
31)
До 5,00
Св. 5,00 до 8,00
Св. 8,00 до 12,0
Св. 12,0 до 16,0
Св. 16,0 до 20,0
Св. 20,0 до 24,0
Св. 24,0 до 32,0
Св. 32,0 до 40,0
20,0
22,0
24,0
28,0
32,0
36,0
44,0
56,0
Св. 5,0 до 6,4
26)
До 1,20
Св. 1,20 до 2,40
Св. 2,40 до 4,00
Св. 4,00 до 5,00
Св. 5,00 до 6,40
Св. 6,40 до 8,00
Св. 8,00 до 10,0
Св. 10,0 до 12,0
Св. 12,0 до 16,0
6,4
7,0
8,0
9,0
10,0
12,0
14,0
16,0
18,0
Св. 20,0 до 24,0
32)
До 6,40
Св. 6,40 до 12,0
Св. 12,0 до 16,0
Св. 16,0 до 20,0
Св. 20,0 до 24,0
Св. 24,0 до 32,0
Св. 32,0 до 40,0
Св. 40,0 до 48,0
24,0
28,0
32,0
36,0
40,0
44,0
56,0
64,0
Св. 6,4 до 8,0
27)
До 2,00
Св. 2,00 до 4,00
Св. 4,00 до 5,00
Св. 5,00 до 6,40
Св. 6,40 до 8,00
Св. 8,00 до 10,0
Св. 10,0 до 12,0
Св. 12,0 до 16,0
8,0
9,0
10,0
11,0
12,0
14,0
18,0
22,0
Св. 24,0 до 32,0
33)
До 8,00
Св.8,00 до 16,0
Св. 16,0 до 20,0
Св. 20,0 до 24,0
Св. 24,0 до 32,0
Св. 32,0 до 40,0
Св. 40,0 до 50,0
Св. 50,0 до 64,0
32,0
36,0
40,0
44,0
50,0
56,0
70,0
90.0
Св. 8,0 до 10,0
28)
До 2,40
Св. 2,40 до 4,00
Св. 4,00 до 6,40
Св. 6,40 до 8,00
Св. 8,00 до 10,0
Св. 10,0 до 12,0
Св. 12,0 до 16,0
Св. 16,0 до 20,0
10,0
11,0
12,0
14,0
16,0
18,0
22,0
28,0
Св. 32,0 до 40,0
34)
До 10,0
Св. 10,0 до 16,0
Св. 16,0 до 24,0
Св. 24,0 до 32,0
Св. 32,0 до 40,0
Св. 40,0 до 50,0
Св. 50,0 до 64,0
Св. 64,0 до 80,0
40,0
44,0
50,0
56,0
64,0
70,0
90,0
110,0
Св. 10,0 до 12,0
29)
До 3,20
Св. 3,20 до 6,40
Св. 6,40 до 8,00
Св. 8,00 до 10,0
12,0
14,0
16,0
18,0
Св. 40,0 до 50,0
35)
До 12,0
Св. 12,0 до 24,0
Св. 24,0 до 32,0
Св. 32,0 до 40,0
50,0
56,0
64,0
70,0
48
Св. 10,0 до 12,0
Св. 12,0 до 16,0
Св. 16,0 до 20,0
Св. 20,0 до 24,0
20,0
24,0
28,0
32,0
Св. 40,0 до 50,0
Св. 50,0 до 64,0
Св. 64,0 до 80,0
Св. 80,0 до 100,0
80,0
90,0
110,0
140,0
Св. 12,0 до 16,0 До 4,00
Св. 4,00 до 8,00
Св. 8,00 до 10,0
Св. 10,0 до 12,0
Св. 12,0 до 16,0
Св. 16,0 до 20,0
Св. 20,0 до 24,0
Св. 24,0 до 32,0
16,0
18,0
20,0
22,0
24,0
28,0
36,0
44,0
Св. 50,0 до 64,0 До 12,0
Св. 12,0 до 24,0
Св. 24,0 до 40,0
Св. 40,0 до 50,0
Св. 50,0 до 64,0
Св. 64,0 до 80,0
Св. 80,0 до 100,0
Св. 100,0 до 120,0
64,0
70,0
80,0
90,0
100,0
120,0
140,0
160,0
Общий припуск
Общий
допуск
элемента
поверхности,
мм
Вид
окончательной
механической
обработки
Ряд
1 2 3 4 5 6 7
1 2 3 4 5 6 7 8 9
До 0,10
1)
Черновая
Чистовая
Тонкая
0,2
0,2
0,2
0,3
0,3
0,3
0,4
0,4
0,4
0,5
0,5
0,5
0,6
0,6
0,6
0,7
0,7
0,7
0,9
0,9
1,0
Св. 0,10
до 0,11
2)
Черновая
Получистовая
Чистовая
Тонкая
0,2
0,2
0,2
0,2
0,3
0,3
0,3
0,4
0,4
0,4
0,4
0,4
0,5
0,5
0,5
0,6
0,6
0,6
0,6
0,6
0,7
0,7
0,7
0.8
0,9
0,9
1,0
1,0
Св. 0,11
до 0,12
3)
Черновая
Получистовая
Чистовая
Тонкая
0,2
0,2
0,2
0,2
0,3
0,3
0,3
0,4
0,4
0,4
0,5
0,5
0,5
0,5
0,5
0,6
0,6
0,7
0,7
0,7
0,7
0,7
0,8
0.8
0,9
0,9
1,0
1,0
Св. 0,12
до 0,14
4)
Черновая
Получистовая
Чистовая
Тонкая
0,2
0,3
0,3
0,3
0,3
0,3
0,4
0,4
0,4
0,5
0,5
0,5
0,5
0,5
0,6
0,6
0,6
0,7
0,7
0,7
0,7
0,8
0,8
0.8
0,9
1,0
1,0
1,0
Св. 0,14
до 0,16
5)
Черновая
Получистовая
Чистовая
Тонкая
0,2
0,3
0,3
0,3
0,3
0,4
0,4
0,4
0,4
0,5
0,5
0,5
0,5
0,6
0,6
0,6
0,6
0,7
0,7
0,7
0,7
0,8
0,8
0.8
0,9
1,0
1,0
1,0
Св. 0,16
до 0,18
6)
Черновая
Получистовая
Чистовая
Тонкая
0,2
0,3
0,3
0,3
0,3
0,4
0,4
0,5
0,4
0,5
0,5
0,5
0,5
0,6
0,6
0,7
0,6
0,7
0,7
0,8
0,7
0,8
0,8
0,9
0,9
1,0
1,0
1,1
Св. 0,18
до 0,20
7)
Черновая
Получистовая
Чистовая
Тонкая
0,2
0,3
0,3
0,3
0,3
0,4
0,4
0,5
0,4
0,5
0,5
0,5
0,5
0,6
0,6
0,7
0,6
0,7
0,7
0,8
0,7
0,8
0,8
0,9
0,9
1,0
1,0
1,1
49
Св. 0,20
до 0,22
8)
Черновая
Получистовая
Чистовая
Тонкая
0,3
0,3
0,4
0,4
0,4
0,4
0,5
0,5
0,4
0,5
0,6
0,6
0,6
0,6
0,7
0,7
0,6
0,7
0,8
0,8
0,8
0,8
0,9
0,9
0,9
1,1
1,1
1,1
Св. 0,22
до 0,24
9)
Черновая
Получистовая
Чистовая
Тонкая
0,3
0,4
0,4
0,4
0,4
0,4
0,5
0,5
0,5
0,6
0,6
0,6
0,6
0,6
0,7
0,7
0,7
0,8
0,8
0,8
0,8
0,8
0,9
0,9
1,0
1,1
1,1
1,2
Таблица 24
на сторону, мм
припусков отливки
8 9 10 11 12 13 14 15 16 17 18
10 11 12 13 14 15 16 17 18 19 20
-
-
-
-
-
-
-
-
-
-
-
-
-
-
-
-
-
-
-
-
-
-
-
-
-
-
-
-
-
-
-
-
-
-
-
-
-
-
-
-
-
-
-
-
-
-
-
-
-
-
-
-
-
-
-
-
-
-
-
-
-
-
-
-
-
-
-
-
-
-
-
-
-
-
-
-
-
1,1
1,3
1,3
1,3
-
-
-
-
-
-
-
-
-
-
-
-
-
-
-
-
-
-
-
-
-
-
-
-
-
-
-
-
-
-
-
-
-
-
-
-
-
-
-
-
1,1
1,3
1,3
1,3
-
-
-
-
-
-
-
-
-
-
-
-
-
-
-
-
-
-
-
-
-
-
-
-
-
-
-
-
-
-
-
-
-
-
-
-
-
-
-
-
1,1
1,3
1,3
1,3
1,3
1,4
1,5
1.5
-
-
-
-
-
-
-
-
-
-
-
-
-
-
-
-
-
-
-
-
-
-
-
-
-
-
-
-
-
-
-
-
-
-
-
-
1,2
1,3
1,3
1,4
1,4
1,5
1,5
1.,6
-
-
-
-
-
-
-
-
-
-
-
-
-
-
-
-
-
-
-
-
-
-
-
-
-
-
-
-
-
-
-
-
-
-
-
-
1,2
1,3
1,3
1,4
1,5
1,5
1,8
1,9
2,1
-
-
-
-
-
-
-
-
-
-
-
-
-
-
-
-
-
-
-
-
-
-
-
-
50
1,4 1.,6 2,1 - - - - - - - -
1,1
1,4
1,4
1,4
1,4
1,6
1,6
1,6
1,8
2,0
2,1
2,1
-
-
-
-
-
-
-
-
-
-
-
-
-
-
-
-
-
-
-
-
-
-
-
-
-
-
-
-
-
-
-
-
1,1
1,4
1,4
1,5
1,4
1,6
1,6
1,7
1,8
2,0
2,1
2,1
2,2
2,4
2,5
2,5
2,6
3,0
3,1
3,3
-
-
-
-
-
-
-
-
-
-
-
-
-
-
-
-
-
-
-
-
-
-
-
-
1 2 3 4 5 6 7 8 9 10
Св. 0,24
до 0,28
10)
Черновая
Получистовая
Чистовая
Тонкая
0,3
0,4
0,4
0,5
0,4
0,5
0,5
0,6
0,5
0,6
0,7
0,7
0,6
0,7
0,8
0,8
0,7
0,8
0,9
0,9
0,8
0,9
1,0
1,0
1,0
1,1
1,2
1,2
1,2
1,4
1,5
1,5
Св. 0,28
до 0,32
11)
Черновая
Получистовая
Чистовая
Тонкая
0,3
0,4
0,5
0,5
0,4
0,5
0,6
0,7
0,5
0,6
0,7
0,8
0,6
0,7
0,8
0,9
0,7
0,8
0,9
1,0
0,8
0,9
1,0
1,1
1,0
1,2
1,2
1,3
1,2
1,5
1,5
1,6
Св. 0,32
до 0,36
12)
Черновая
Получистовая
Чистовая
Тонкая
0,3
0,5
0,5
0,6
0,5
0,6
0,7
0,7
0,5
0,7
0,8
0,8
0,7
0,8
0,9
0,9
0,8
0,9
1,0
1,0
0,9
1,0
1,1
1,1
1,1
1,2
1,3
1,3
1,3
1,5
1,6
1,6
Св. 0,36
до 0,40
13)
Черновая
Получистовая
Чистовая
Тонкая
0,4
0,5
0,6
0,6
0,5
0,6
0,7
0,8
0,6
0,7
0,8
0,8
0,7
0,8
0,9
0,9
0,8
0,9
1,0
1,1
0,9
1,0
1,1
1,1
1,1
1,2
1,3
1,4
1,3
1,5
1,6
1,6
Св. 0,40
до 0,44
14)
Черновая
Получистовая
Чистовая
Тонкая
0,4
0,6
0,6
0,7
0,5
0,7
0,7
0,8
0,6
0,8
0,9
0,9
0,7
0,9
1,0
1,0
0,8
1,0
1,1
1,1
0,9
1,1
1,2
1,2
1,1
1,3
1,4
1,4
1,3
1,6
1,7
1,7
Св. 0,44
до 0,50
15)
Черновая
Получистовая
Чистовая
Тонкая
0,5
0,6
0,7
0,8
0,5
0,7
0,8
0,9
0,7
0,8
0,9
1,0
0,8
0,9
1,0
1,1
0,9
1,0
1,1
1,2
1,0
1,1
1,2
1,3
1,2
1,3
1,4
1,5
1,4
1,6
1,7
1,8
Св. 0,50
до 0,56
16)
Черновая
Получистовая
Чистовая
Тонкая
0,5
0,7
0,8
0,9
0,6
0,8
0,9
1,0
0,7
0,9
1,0
1,1
0,8
1,0
1,1
1,2
0,9
1,1
1,2
1,3
1,1
1,2
1,3
1,4
1,2
1,4
1,5
1,6
1,4
1,7
1,8
1,9
51
Св. 0,56
до 0,64
17)
Черновая
Получистовая
Чистовая
Тонкая
0,5
0,8
0,9
1,0
0,7
0,9
1,0
1,1
0,8
1,0
1,1
1,2
0,9
1,1
1,2
1,3
1,0
1,2
1,3
1,4
1,1
1,3
1,4
1,5
1,3
1,5
1,6
1,7
1,5
1,8
1,9
2,0
Св. 0,64
до 0,70
18)
Черновая
Получистовая
Чистовая
Тонкая
0,6
0,8
0,9
1,1
0,7
0,9
1,1
1,1
0,8
1,1
1,1
1,3
0,9
1,2
1,3
1,4
1,0
1,3
1,4
1,4
1,1
1,4
1,4
1,6
1,4
1,6
1,6
1,8
1,5
1,9
1,9
2,1
Св. 0,70
до 0,80
19)
Черновая
Получистовая
Чистовая
Тонкая
0,6
0,9
1,1
1,2
0,8
1,1
1,2
1,3
0,8
1,2
1,3
1,4
0,9
1,3
1,4
1,5
1,1
1,4
1,5
1,6
1,1
1,5
1,6
1,7
1,4
1,7
1,8
1,9
1,6
2,0
2,1
2,2
11 12 13 14 15 16 17 18 19 20
1,4
1,6
1,7
1,7
1,8
2,0
2,1
2,2
2,2
2,4
2,5
2,6
2,7
3,0
3,2
3,3
-
-
-
-
-
-
-
-
-
-
-
-
-
-
-
-
-
-
-
-
-
-
-
-
1,4
1,7
1,7
1,8
1,8
2,1
2,2
2,3
2,2
2,4
2,6
2,7
2,7
3,1
3,2
3,4
3,3
3,6
3,6
3,9
-
-
-
-
-
-
-
-
-
-
-
-
-
-
-
-
-
-
-
-
1,5
1,7
1,8
1,8
1,9
2,1
2,3
2,3
2,3
2,5
2,7
2,7
2,7
3,1
3,3
3,4
3,3
3,6
3,8
3,9
-
-
-
-
-
-
-
-
-
-
-
-
-
-
-
-
-
-
-
-
1,5
1,7
1,8
1,9
1,9
2,1
2,3
2,4
2,3
2,5
2,7
2,8
2,8
3,2
3,3
3,4
3,3
3,7
3,8
4,0
4,3
4,8
5,0
5,1
-
-
-
-
-
-
-
-
-
-
-
-
-
-
-
-
1,5
1,8
1,9
1,9
1,9
2,2
2,4
2,4
2,3
2,6
2,7
2,8
2,8
3,1
3,4
3,4
3,4
3,6
3,9
4,0
4,3
4,8
5,0
5,1
-
-
-
-
-
-
-
-
-
-
-
-
-
-
-
-
1,6
1,8
1,9
2,0
2,0
2,2
2,4
2,5
2,4
2,6
2,8
2,9
2,8
3,3
3,5
3,6
3,4
3,8
3,9
4,1
4,4
4,8
5,2
5,3
5,3
5,8
6,2
6,3
-
-
-
-
-
-
-
-
-
-
-
-
1,6
1,9
2,0
2,0
2,3
2,5
2,4
2,7
2,9
2,9
3,3
3,4
3,4
3,8
4,0
4,4
4,9
5,1
5,5
5,8
6,1
-
-
-
-
-
-
-
-
-
52
2,1 2,6 3,0 3,6 4,3 5,5 6,3 - - -
1,7
2,0
2,1
2,2
2,1
2,4
2,6
2,7
2,4
2,8
3,0
3,1
2,9
3,4
3,6
3,8
3,5
3,9
4,1
4,3
4,4
5,0
5,3
5,4
5,5
6,0
6,3
6,5
6,5
7,1
7,3
7,5
-
-
-
-
-
-
-
-
1,7
2,1
2,2
2,3
2,1
2,4
2,6
2,8
2,5
2,8
3,1
3,1
3,0
3,5
3,6
3,9
3,4
3,9
4,1
4,4
4,5
5,0
5,3
5,6
5,4
6,0
6,3
6,5
6,5
7,1
7,5
7,8
8,5
9,3
9,8
9,8
-
-
-
-
1,8
2,1
2,3
2,4
2,2
2,5
2,8
2,9
2,6
2,9
3,1
3,4
3,1
3,6
3,8
4,0
3,6
4,0
4,3
4,5
4,6
5,2
5,4
5,8
5,6
6,2
6,5
6,7
6,5
7,3
7,5
7,8
8,5
9,3
9,8
10,0
-
-
-
-
Св. 0,80
до 0,90
20)
Черновая
Получистовая
Чистовая
Тонкая
0,7
1,1
1,2
1,4
0,8
1,2
1,3
1,4
0,9
1,3
1,4
1,6
1,0
1,4
1,5
1,6
1,1
1,5
1,6
1,8
1,2
1,6
1,7
1,9
1,4
1,8
1,9
2,1
1,6
2,1
2,2
2,4
Св. 0,90
до 1,00
21)
Черновая
Получистовая
Чистовая
Тонкая
0,8
1,2
1,3
1,5
0,9
1,3
1,4
1,6
1,0
1,4
1,5
1,7
1,1
1,5
1,6
1,8
1,2
1,6
1,7
1,9
1,3
1,7
1,8
2,0
1,5
1,9
2,0
2,2
1,7
2,1
2,3
2,5
Св. 1,00
до 1,10
22)
Черновая
Получистовая
Чистовая
Тонкая
0,8
1,1
1,4
1,6
0,9
1,3
1,4
1,7
1,1
1,4
1,6
1,8
1,2
1,4
1,6
1,9
1,3
1,6
1,8
2,0
1,4
1,6
1,9
2,1
1,6
1,9
2,1
2,3
1,8
2,2
2,4
2,5
Св. 1,10
до 1,20
23)
Черновая
Получистовая
Чистовая
Тонкая
0,9
1,3
1,5
1,7
1,0
1,4
1,6
1,8
1,1
1,5
1,7
1,9
1,2
1,6
1,8
2,0
1,3
1,7
1,9
2,1
1,4
1,8
2,0
2,1
1,6
2,0
2,2
2,4
1,8
2,3
2,5
2,7
Св. 1,20
до 1,40
24)
Черновая
Получистовая
Чистовая
Тонкая
1,1
1,5
1,8
1,9
1,2
1,6
1,9
2,0
1,3
1,7
1,9
2,1
1,4
1,8
2,1
2,2
1,5
1,9
2,2
2,3
1,6
2,0
2,3
2,4
1,8
2,2
2,5
2,6
2,0
2,5
2,8
2,9
Св. 1,40
до 1,60
25)
Черновая
Получистовая
Чистовая
Тонкая
1,2
1,7
1,9
2,2
1,3
1,8
2,1
2,3
1,4
1,9
2,2
2,4
1,5
2,0
2,3
2,5
1,6
2,1
2,4
2,6
1,7
2,2
2,5
2,7
1,9
2,4
2,6
2,9
2,1
2,7
3,0
3,1
Св. 1,60
до 1,80
26)
Черновая
Получистовая
Чистовая
Тонкая
1,2
1,8
2,1
2,3
1,3
1,9
2,2
2,4
1,4
2,0
2,3
2,5
1,5
2,1
2,4
2,6
1,6
2,2
2,5
2,7
1,7
2,3
2,6
2,8
2,0
2,6
3,0
3,3
2,1
2,8
3,1
3,4
Св. 1,80
до 2,00
Черновая
Получистовая
1,3
1,9
1,4
2,1
1,5
2,2
1,6
2,3
1,7
2,4
1,8
2,5
2,0
2,6
2,2
2,8
53
27) Чистовая
Тонкая
2,3
2,6
2,4
2,7
2,5
2,8
2,6
2,9
2,7
3,0
2,8
3,1
3,0
3,3
3,3
3,6
Св. 2,00
до 2,20
28)
Черновая
Получистовая
Чистовая
Тонкая
1,5
2,1
2,5
2,9
1,6
2,3
2,6
3,0
1,7
2,4
2,7
3,1
1,8
2,4
2,8
3,1
1,9
2,5
2,9
3,3
2,0
2,7
3,0
3,4
2,2
2,8
3,3
3,6
2,4
3,2
3,6
3,9
1,8
2,3
2,4
2,6
2,2
2,7
2,9
3,1
2,6
3,1
3,4
3,4
3,2
3,7
3,9
4,1
3,7
4,1
4,4
4,6
4,6
5,3
5,6
5,8
5,6
6,3
6,7
6,9
6,7
7,3
7,8
8,0
8,5
9,5
9,8
10,5
10,5
11,5
12,0
12,5
1,9
2,4
2,5
2,7
2,3
2,7
3,0
3,1
2,7
3,2
3,5
3,6
3,2
3,8
4,0
4,3
3,7
4,3
4,5
4,8
4,8
5,3
5,8
6,0
5,6
6,3
6,7
6,9
6,7
7,5
7,8
8,0
8,8
9,5
10,0
10,5
10,5
11,5
12,0
12,5
2,0
2,4
2,6
2,7
2,4
2,8
3,1
3,3
2,7
3,2
3,5
3,7
3,3
3,8
4,1
4,4
3,8
4,3
4,6
4,9
4,8
5,3
5,8
6,0
5,8
6,3
6,7
7,1
6,7
7,5
7,8
8,3
8,8
9,5
10,0
10,5
10,5
11,5
12,5
12,5
2,0
2,5
2,7
2,8
2,4
2,9
3,1
3,4
2,8
3,4
3,6
3,8
3,4
3,9
4,3
4,4
3,8
4,4
4,8
4,9
4,8
5,4
5,8
6,2
5,8
6,5
6,9
7,1
6,9
7,5
8,0
8,3
8,8
9,8
10,0
10,5
11,0
12,0
12,5
12,5
2,1
2,7
3,0
3,2
2,5
3,1
3,4
3,7
2,9
3,4
3,9
4,0
3,5
4,1
4,5
4,8
3,9
4,6
5,0
5,1
4,9
5,6
6,1
6,5
6,0
6,7
7,1
7,5
6,9
7,8
8,3
8,5
9,0
9,8
10,5
11,0
11,0
12,0
12,5
13,0
2,3
2,9
3,1
3,4
2,7
3,3
3,6
3,9
3,1
3,6
4,1
4,3
3,6
4,3
4,6
5,0
4.0
4,8
5,1
5,4
5,0
5,8
6,3
6,7
6,0
6,9
7,3
7,8
7,1
8,0
8,5
8,8
9,0
10,0
10,5
11,0
11,0
12,0
13,0
13,5
2,3
3,0
3,3
3,6
2,7
3,5
3,8
4,0
3,2
3,8
4,3
4,4
3,7
4,4
4,8
5,2
4.1
4,9
5,3
5,6
5,2
6,0
6,5
6,9
6,2
7,1
7,5
7,8
7,1
8,0
8,5
9,0
9,0
10,0
11,0
11,0
11,0
12,5
13,0
13,5
2,4
3,1
3,6
3,8
2,8
3,6
4,0
4,3
3,3
4,0
4,4
4,8
3,8
4,6
5,0
5,5
4,3
5,0
5,4
5,8
5,1
6,1
6,7
7,1
6,1
7,1
7,8
8,0
7,3
8,3
8,8
9,3
9,3
10,5
11,0
11,5
11,0
12,5
13,0
13,5
2,6
3,4
3,8
4,1
3,0
3,8
4,3
4,6
3,4
4,1
4,6
5,0
3,9
4,8
5,1
5,6
4,4
5,3
5,8
6,1
5,5
6,3
6,9
7,3
6,3
7,3
8,0
8,3
7,3
8,5
9,0
9,5
9,5
10,5
11,0
12,0
11,5
12,5
13,5
14,0
54
Св. 2,20
до 2,40
29)
Черновая
Получистовая
Чистовая
Тонкая
1,6
2,4
2,7
3,1
1,7
2,5
2,8
3,1
1,8
2,6
2,9
3,3
1,9
2,6
3,1
3,4
2,0
2,8
3,2
3,4
2,1
2,9
3,3
3,6
2,3
3,1
3,5
3,8
2,5
3,4
3,8
4,1
Св. 2,40
до 2,80
30)
Черновая
Получистовая
Чистовая
Тонкая
1,8
2,6
3,0
3,5
1,9
2,7
3,2
3,6
1,9
2,8
3,3
3,7
2,1
2,9
3,4
3,8
2,2
3,0
3,5
3,8
2,3
3,1
3,6
3,9
2,5
3,3
3,8
4,1
2,6
3,6
4,0
4,4
Св. 2,80
до 3,20
31)
Черновая
Получистовая
Чистовая
Тонкая
1,9
3,0
3,4
3,8
2,1
3,1
3,6
3,9
2,2
3,1
3,6
4,0
2,3
3,3
3,8
4,1
2,4
3,4
3,9
4,3
2,5
3,4
4,0
4,3
2,6
3,6
4,1
4,5
2,9
4,0
4,5
4,8
Св. 3,20
до 3,60
32)
Черновая
Получистовая
Чистовая
Тонкая
2,2
3,3
3,9
4,3
2,3
3,4
4,0
4,4
2,4
3,4
4,1
4,4
2,5
3,6
4,3
4,5
2,6
3,6
4,3
4,6
2,7
3,8
4,4
4,8
2,9
4,0
4,6
4,9
3,1
4,3
4,9
5,3
Св. 3,60
до 4,00
33)
Черновая
Получистовая
Чистовая
Тонкая
2,4
3,6
4,3
4,8
2,5
3,8
4,4
4,9
2,6
3,9
4,4
5,0
2,7
4,0
4,5
5,2
2,8
4,1
4,6
5,3
2,9
4,3
4,8
5,3
3,2
4,4
4,9
5,4
3,4
4,8
5,3
5,8
Св. 4,00
до 4,40
34)
Черновая
Получистовая
Чистовая
Тонкая
2,5
3,8
4,5
4,9
2,6
3,9
4,6
5,0
2,7
4,0
4,8
5,2
2,8
4,1
4,8
5,3
2,9
4,3
4,9
5,3
3,0
4,3
5,0
5,5
3,3
4,5
5,1
5,6
3,5
4,8
5,4
6,0
Св. 4,40
до 5,00
35)
Черновая
Получистовая
Чистовая
Тонкая
2,9
4,3
5,0
5,6
3,0
4,4
5,1
5,8
3,1
4,4
5,3
5,8
3,1
4,5
5,3
6,0
3,3
4,6
5,4
6,0
3,4
4,8
5,6
6,2
3,6
4,9
5,8
6,3
3,8
5,3
6,0
6,7
Св. 5,00
до 5,60
36)
Черновая
Получистовая
Чистовая
Тонкая
-
-
-
-
3,3
4,9
5,8
6,3
3,4
5,0
5,8
6,5
3,4
5,2
6,0
6,5
3,6
5,1
6,0
6,7
3,6
5,3
6,2
6,7
3,9
5,4
6,3
6,9
4,1
5,8
6,7
7,3
Св. 5,60
до 6,40
37)
Черновая
Получистовая
Чистовая
Тонкая
-
-
-
-
3,8
5,1
6,1
6,9
3,9
5,3
6,3
7,1
4,0
5,3
6,3
7,1
4,1
5,4
6,5
7,3
4,3
5,6
6,5
7,3
4,4
5,8
6,7
7,5
4,6
6,0
7,1
7,8
2,7 3,1 3,4 4,0 4,5 5,4 6,5 7,5 9,5 11,5
55
3,6
3,9
4,3
4,0
4,4
4,8
4,4
4,9
5,1
5,0
5,5
5,8
5,4
6,0
6,3
6,5
7,1
7,5
7,5
8,3
8,5
8,8
9,3
9,8
11,0
11,5
12,0
13,0
13,5
14,0
2,9
3,8
4,3
4,6
3,3
4,3
4,8
5,2
3,6
4,6
5,2
5,4
4,1
5,1
5,8
6,1
4,6
5,6
6,1
6,7
5,6
6,7
7,5
8,0
6,7
7,8
8,5
9,0
7,8
9,0
9,5
10.0
9,8
11,0
11,5
12,5
11,5
13,0
14,0
14,5
3,1
4,1
4,6
5,0
3,4
4,6
5,1
5,4
3,9
5,0
5,6
5,8
4,4
5,6
6,1
6,5
4,9
6,0
6,7
7,1
5,8
7,1
7,8
8,3
6,9
8,3
8,8
9,3
7,8
9,3
9,8
10,5
9,8
11,5
12,0
12,5
12,0
13,5
14,5
15,0
3,3
4,5
5,2
5,5
3,6
4,9
5,6
6,0
4,1
5,3
6,0
6,3
4,6
5,8
6,5
7,1
5,2
6,3
7,1
7,5
6,2
7,5
8,3
8,8
7,1
8,5
9,3
9,8
8,0
9,5
10,5
11,0
10,0
11,5
12,5
13,0
12,0
14,0
15,0
15,5
3,6
4,9
5,5
6,0
3,9
5,3
6,0
6,5
4,3
5,6
6,3
6,9
4,8
6,3
6,9
7,5
5,3
6,7
7,5
8,0
6,3
8,0
8,8
9.3
7,3
9,0
9,8
10,5
8,3
9,8
10,5
11,5
10,5
12,0
13,0
13,5
12,5
14,0
15,0
15,5
3,7
5,0
5,8
6,2
4,0
5,5
6,1
6,7
4,4
5,8
6,7
7,1
4,9
6,3
7,3
7,8
5,5
6,9
7,8
8,3
6,5
8,0
9,0
9,5
7,5
9,0
9,8
10,5
8,5
10,0
11,0
11,5
10,5
12,0
13,0
14,0
12,5
14,5
15,5
16,0
4,0
5,5
6,3
6,9
4,4
5,8
6,7
7,3
4,8
6,3
7,1
7,8
5,3
6,9
7,8
8,5
5,8
7,3
8,3
9,0
6,7
8,5
9,5
10,0
7,8
9,5
10,5
11,0
8,8
10,5
11,5
12,0
11,0
12,5
14,0
14,5
13,0
14,5
16,0
16,5
4,3
6,0
6,9
7,5
4,8
6,3
7,3
8,0
5,2
6,7
7,8
8,3
5,6
7,3
8,3
9,0
6,2
8,0
8,8
9,5
7,1
9,0
10,0
11,0
8,0
9,8
11,0
12,0
9,0
11,0
12,0
13,0
11,0
13,0
14,5
15,0
13,0
15,5
16,5
17,5
4,8
6,3
7,3
8,0
5,1
6,7
7,8
8,5
5,6
7,1
8,3
9,0
6,2
7,8
8,8
9,8
6,5
8,3
9,3
10,0
7,5
9,3
10,5
11,5
8,5
10,5
11,5
12,5
9,5
11,5
12,5
13,5
11,5
13,5
15,0
16,0
13,5
15,5
17,0
18,0
56
Св. 6,40
до 7,00
38)
Черновая
Получистов
ая
Чистовая
Тонкая
-
-
-
-
-
-
-
-
4,3
5,8
6,9
7,8
4,3
6,0
7,1
7,8
4,4
6,0
7,1
7,8
4,5
6,2
7,3
8,0
4,8
6,3
7,5
8,3
4,9
6,7
7,8
8,5
Св. 7,00
до 8,00
39)
Черновая
Получистов
ая
Чистовая
Тонкая
-
-
-
-
-
-
-
-
4,8
6,5
8,0
8,5
4,8
6,5
8,0
8,8
4,9
6,7
8,0
8,8
5,0
6,7
8,3
8,8
5,1
6,9
8,5
9,0
5,5
7,3
8,8
9,3
Св. 8,00
до 9,00
40)
Черновая
Получистов
ая
Чистовая
Тонкая
-
-
-
-
-
-
-
-
-
-
-
-
5,3
7,3
9,0
9,8
5,4
7,5
9,0
9,8
5,6
7,5
9,3
9,8
5,8
7,8
9,3
10,0
6,0
8,0
9,8
10,5
Св. 9,00
до 10,00
41)
Черновая
Получистов
ая
Чистовая
Тонкая
-
-
-
-
-
-
-
-
-
-
-
-
6,0
8,3
9,8
11,0
6,0
8,3
9,8
11,0
6,2
8,5
9,8
11,0
6,3
8,5
10,0
11,5
6,5
9,0
10,5
11,5
Св. 10,00
до 11,00
42)
Черновая
Получистов
ая
Чистовая
Тонкая
-
-
-
-
-
-
-
-
-
-
-
-
-
-
-
-
6,5
8,5
10,0
11,0
6,5
8,8
10,0
11,5
6,7
8,8
10,5
11,5
6,9
9,3
10,5
12,0
Св. 11,00
до 12,00
43)
Черновая
Получистов
ая
Чистовая
Тонкая
-
-
-
-
-
-
-
-
-
-
-
-
-
-
-
-
7,1
9,3
11,0
12,5
7,3
9,5
11,0
12,5
7,5
9,5
11,5
13,0
7,5
9,8
11,5
13,0
Св. 12,00
до 14,00
44)
Черновая
Получистов
ая
Чистовая
Тонкая
-
-
-
-
-
-
-
-
-
-
-
-
-
-
-
-
-
-
-
-
8,5
11,0
12,5
14,5
8,5
11,5
13,0
14,5
8,8
11,5
13,0
15,0
Св. 14,00
до 16,00
45)
Черновая
Получистов
ая
Чистовая
Тонкая
-
-
-
-
-
-
-
-
-
-
-
-
-
-
-
-
-
-
-
-
9,5
12,0
15,0
16,5
9,5
12,5
15,0
17,0
9,8
12,5
15,5
17,0
Св. 16,00
до 18,00
46)
Черновая
Получистов
ая
Чистовая
Тонкая
-
-
-
-
-
-
-
-
-
-
-
-
-
-
-
-
-
-
-
-
-
-
-
-
10,5
13,5
15,5
18,0
11,0
14,0
16,0
18,0
57
Продолжение табл.24
5,2
6,9
8,0
8,8
5,4
7,3
8,5
9,3
6,0
7,5
8,8
9,5
6,5
8,3
9,5
10,5
6,9
8,8
9,8
11,0
8,0
9,8
11,0
12,0
9,0
11,0
12,0
13,0
9,8
12,0
13,0
14,0
12,0
14,0
15,5
16,5
14,0
16,0
17,5
18,5
5,6
7,5
9,0
9,5
6,0
7,8
9,5
10,0
6,5
8,3
9,8
10,5
6,9
8,8
10,5
11,5
7,5
9,3
11,0
11,5
8,5
10,5
12,0
13,0
9,5
11,5
13,0
14,0
10,5
12,5
14,0
15,0
12,5
14,5
16,5
17,5
14,5
17,0
18,5
19,5
6,1
8,3
9,8
10,5
6,5
8,8
10,5
11,0
6,9
9,0
10,5
11,5
7,5
9,8
11,5
12,5
8,0
10,0
12,0
13,0
9,0
11,0
13,0
14,0
9,8
12,0
14,0
15,0
11,0
13,5
15,0
16,0
13,0
15,5
17,5
18,5
15,0
17,5
19,5
20,5
6,7
9,0
10,5
12,0
7,1
9,5
11,0
12,5
7,5
9,8
11,5
12,5
8,0
10,5
12,0
13,5
8,5
11,0
12,5
14,0
9,5
12,0
14,0
15,0
10,5
13,0
15,0
16,0
11,5
14,0
16,0
17,0
13,5
16,5
18,0
19,5
15,5
18,5
20,5
22,0
7,1
9,3
11,0
12,0
7,5
9,8
11,5
12,5
8,0
10,0
12,0
13,0
8,5
10,5
12,5
13,5
9,0
11,0
13,0
14,0
9,8
12,5
14,0
15,5
11,0
13,5
15,0
16,5
12,0
14,5
16,0
17,5
14,0
16,5
18,5
19,5
16,0
18,5
20,5
22,0
7,8
10,0
12,0
13,5
8,3
10,5
12,5
14,0
8,5
11,0
12,5
14,5
9,0
11,5
13,5
15,0
9,5
12,0
14,0
15,5
10,5
13,0
15,0
16,5
11,5
14,0
16,0
17,5
12,5
15,0
17,0
19,0
14,5
17,5
19,5
21,0
16,5
19,5
21,0
23,5
9,0
12,0
13,5
15,0
9,5
12,0
14,0
15,5
9,8
12,5
14,5
16,0
10,5
13,0
15,0
16,5
11,0
13,5
15,5
17,0
12,0
15,0
16,5
18,5
13,0
16,0
17,5
19,5
14,0
17,0
18,5
20,5
16,0
19,0
21,0
23,0
18,0
21,0
23,0
25,0
10,0
13,0
15,5
17,5
10,5
13,5
16,0
18,0
11,0
13,5
16,5
18,0
11,5
14,5
17,0
19,0
12,0
15,0
17,5
19,5
13,0
16,0
19,0
20,5
14,0
17,0
20,0
22,0
15,0
18,0
21,0
22,5
17,0
20,0
23,0
25,0
19,0
22,0
25,0
27,0
11,0
14,0
16,0
18,5
11,5
14,5
16,5
19,0
12,0
15,0
17,0
19,5
12,5
15,5
17,5
20,0
13,0
16,0
18,0
20,5
14,0
17,0
19,5
22,0
15,0
18,0
20,5
22,5
16,0
19,0
21,0
24,0
18,0
21,0
23,5
26,0
20,0
23,5
26,0
28,0
58
Св. 18,00
до 20,00
47)
Черновая
Получистов
ая
Чистовая
Тонкая
-
-
-
-
-
-
-
-
-
-
-
-
-
-
-
-
-
-
-
-
-
-
-
-
11,5
14,5
17,5
19,5
11,5
15,0
17,5
20,0
Св. 20,00
до 22,00
48)
Черновая
Получистов
ая
Чистовая
Тонкая
-
-
-
-
-
-
-
-
-
-
-
-
-
-
-
-
-
-
-
-
-
-
-
-
-
-
-
-
13,0
16,5
19,5
21,0
Св. 22,00
до 24,00
49)
Черновая
Получистов
ая
Чистовая
Тонкая
-
-
-
-
-
-
-
-
-
-
-
-
-
-
-
-
-
-
-
-
-
-
-
-
-
-
-
-
14,0
17,5
21,0
23,5
Св. 24,00
до 28,00
50а)
Черновая
Получистов
ая
Чистовая
Тонкая
-
-
-
-
-
-
-
-
-
-
-
-
-
-
-
-
-
-
-
-
-
-
-
-
-
-
-
-
-
-
-
-
Св. 28,00
до 32,00
51а)
Черновая
Получистов
ая
Чистовая
Тонкая
-
-
-
-
-
-
-
-
-
-
-
-
-
-
-
-
-
-
-
-
-
-
-
-
-
-
-
-
-
-
-
-
Св. 32,00
до 36,00
52а)
Черновая
Получистов
ая
Чистовая
Тонкая
-
-
-
-
-
-
-
-
-
-
-
-
-
-
-
-
-
-
-
-
-
-
-
-
-
-
-
-
-
-
-
-
Св. 36,00
до 40,00
53а)
Черновая
Получистов
ая
Чистовая
Тонкая
-
-
-
-
-
-
-
-
-
-
-
-
-
-
-
-
-
-
-
-
-
-
-
-
-
-
-
-
-
-
-
-
Св. 40,00
до 44,00
54а)
Черновая
Получистов
ая
Чистовая
Тонкая
-
-
-
-
-
-
-
-
-
-
-
-
-
-
-
-
-
-
-
-
-
-
-
-
-
-
-
-
-
-
-
-
Св. 44,00
до 50,00
55а)
Черновая
Получистов
ая
-
-
-
-
-
-
-
-
-
-
-
-
-
-
-
-
-
-
-
-
-
-
-
-
59
Чистовая
Тонкая
- - - - - - - -
Продолжение табл.
12,0
15,0
18,0
20,0
12,5
15,5
18,5
20,5
12,5
16,0
18,5
21,0
13,0
16,5
19,5
22,0
13,5
17,0
20,0
22,0
14,5
18,0
21,0
23,5
15,5
19,0
22,0
24,0
16,5
20,0
23,0
25,0
18,5
22,5
25,0
28,0
20,5
24,0
28,0
30,0
13,5
16,5
19,5
22,0
13,5
17,0
20,0
22,0
14,0
17,5
20,5
22,5
14,5
18,0
21,0
23,5
15,0
18,5
21,0
24,0
16,0
19,5
22,5
25,0
17,0
20,5
23,5
26,0
18,0
22,0
25,0
27,0
20,0
24,0
27,0
29,0
22,0
26,0
29,0
31,5
14,5
18,0
21,0
24,0
15,0
18,0
22,0
24,0
15,0
18,5
22,0
25,0
15,5
19,0
22,5
25,0
16,0
19,5
23,0
26,0
17,0
21,0
24,0
27,0
18,0
22,0
25,0
28,0
19,0
23,0
26,5
29,0
21,0
25,0
29,0
31,5
23,0
27,0
30,5
33,5
-
-
-
-
17,0
21,0
24,0
26,5
17,5
21,0
24,0
27,0
18,0
22,0
25,0
28,0
18,5
22,5
25,0
28,0
19,5
23,5
26,5
29,0
20,5
25,0
28,0
30,5
21,0
26,0
29,0
31,5
23,5
28,0
30,5
33,5
25,0
30,0
33,5
35,5
-
-
-
-
19,0
23,5
26,5
30,5
19,5
24,0
27,0
30,5
20,0
25,0
28,0
31,5
20,5
25,0
28,0
32,5
22,0
26,5
29,0
33,5
22,5
27,0
30,5
34,5
23,5
28,0
31,5
35,5
26,0
30,5
33,5
37,5
28,0
32,5
35,5
40,0
-
-
-
-
21,0
26,5
30,5
33,5
22,5
27,0
30,5
34,5
22,5
27,0
31,5
34,5
23,0
28,0
31,5
35,5
24,0
29,5
33,5
36,5
25,0
30,0
34,5
37,5
26,0
31,5
35,5
39,0
28,0
33,5
37,5
41,0
30,0
35,5
40,0
42,5
-
-
-
-
23,5
29,0
32,5
37,5
24,0
30,0
33,5
37,5
25,0
30,5
34,5
39,0
26,0
31,5
35,5
40,0
25,0
30,0
34,5
37,5
27,0
32,5
36,5
41,0
28,0
33,5
37,5
42,5
30,0
35,5
40,0
42,5
32,5
37,5
42,5
47,5
-
-
-
-
-
-
-
-
26,0
32,5
36,5
39,0
26,5
33,5
37,5
40,0
27,0
34,5
37,5
40,0
28,0
35,5
39,0
41,0
29,0
36,5
40,0
42,5
30,0
37,5
41,0
44,0
32,5
39,0
44,0
46,0
34,5
41,0
46,0
47,5
-
-
-
-
-
-
-
-
30,0
36,5
41,0
44,0
30,0
37,5
42,5
44,0
30,5
37,5
42,5
45,0
31,5
39,0
44,0
46,0
32,5
40,0
45,0
47,5
33,5
41,0
46,0
47,5
35,5
42,5
47,5
50,0
37,5
45,0
50,0
53,0
60
Св. 50,00
до 56,00
56а)
Черновая
Получистов
ая
Чистовая
Тонкая
-
-
-
-
-
-
-
-
-
-
-
-
-
-
-
-
-
-
-
-
-
-
-
-
-
-
-
-
-
-
-
-
Св. 56,00
до 64,00
57а)
Черновая
Получистов
ая
Чистовая
Тонкая
-
-
-
-
-
-
-
-
-
-
-
-
-
-
-
-
-
-
-
-
-
-
-
-
-
-
-
-
-
-
-
-
Св. 64,00
до 70,00
58а)
Черновая
Получистов
ая
Чистовая
Тонкая
-
-
-
-
-
-
-
-
-
-
-
-
-
-
-
-
-
-
-
-
-
-
-
-
-
-
-
-
-
-
-
-
Св. 70,00
до 80,00
59а)
Черновая
Получистов
ая
Чистовая
Тонкая
-
-
-
-
-
-
-
-
-
-
-
-
-
-
-
-
-
-
-
-
-
-
-
-
-
-
-
-
-
-
-
-
отливки, приведенных в табл. 21 для погрешностей размеров и в табл.
22 для погрешностей формы и расположения поверхностей детали и
отливки. Окончательно принимают значение припуска,
соответствующее более точной обработке.
В табл. 24 приведены общие припуски для отливок,
обрабатываемых при среднем уровне точности металлорежущего
оборудования. При повышенном или пониженном уровне точности
оборудования, классификация которого по уровню точности приведена
в табл. 25 [5, табл. Ж.1], следует назначать соответственно увеличенные
или уменьшенные припуски. При повышенном или высоком уровне
точности обработки следует применять значения припусков,
соответствующие интервалам общих допусков (табл. 24) на одну или
две строки выше интервалов действительного допуска, при
пониженном уровне точности – на одну строку ниже интервала
действительного допуска.
Для отливок мелкосерийного и единичного производства
допускается назначать увеличенные значения припусков,
61
соответствующие интервалам общих припусков, приведенным в табл.
24, соответственно, на 1 или 2 строки ниже интервала действительного
допуска.
Окончание табл.24
-
-
-
-
-
-
-
-
-
-
-
-
33,5
42,5
47,5
50,0
33,5
42,5
47,5
50,0
34,5
44,0
49,0
51,5
35,5
44,0
50,0
53,5
36,5
45,0
50,0
53,0
39,0
47,5
53,0
56,0
41,0
50,0
54,5
58,0
-
-
-
-
-
-
-
-
-
-
-
-
39,0
46,0
50,0
53,0
39,0
46,0
50,0
53,0
40,0
47,5
51,5
54,5
41,0
47,5
53,0
54,5
42,5
49,0
53,0
56,0
44,0
51,5
56,0
58,0
46,0
53,0
58,0
60,0
-
-
-
-
-
-
-
-
-
-
-
-
-
-
-
-
42,5
50,0
56,0
58,0
42,5
51,5
56,0
60,0
44,0
51,5
58,0
60,0
45,0
53,0
58,0
61,5
47,5
56,0
61,5
65,0
49,0
58,0
63,0
67,0
-
-
-
-
-
-
-
-
-
-
-
-
-
-
-
-
47,5
56,0
61,5
65,0
47,5
56,0
63,0
67,0
49,0
58,0
65,0
69,0
50,0
58,0
65,0
69,0
51,5
61,5
67,0
71,0
54,5
63,0
69,0
73,0
Таблица 25
Уровень точности обработки, достигаемой в зависимости от
технического уровня технологии механообработки
Характеристика
металлообрабатывающего
оборудования
Уровень точности обработки при
степени точности станков
нормальной высокой
Автоматизированное оборудование,
оснащенное устройствами для
стабилизации и управления точностью
обработки
- Высокая
Автоматизированное оборудование
(агрегатные станки с ЧПУ,
автоматические линии из агрегатных
станков с ЧПУ и гибких
производственных модулей и т.п.)
Средняя Повышенная
Неавтоматизированное оборудование Пониженная средняя
62
(станки с ручным управлением)
2.5. ПРИМЕРЫ ОПРЕДЕЛЕНИЯ ПАРАМЕТРОВ
ОТЛИВКИ ПО ГОСТ Р 53464–2009
2.5.1. Пример 1- тело вращения. Деталь «Ступица»[ 1 ]* )
1. Выбор баз механической обработки
На чертеже заготовки должны присутствовать базы черновой
обработки. К сожалению, часто такая информация на чертежах отливок
отсутствует, хотя без них припуски на механическую обработку по
ГОСТ Р 53464–2009 назначить правильно нельзя.
При выборе баз механической обработки предлагается
использовать методику, изложенную в работе [16]. На чертеже детали
буквами помечают поверхности, на которые необходимо назначить
припуски на обработку. Для тел вращения базы механической обработки
следует определять отдельно для плоских поверхностей и для
поверхностей вращения. Определение баз механической обработки
плоских поверхностей (на рис. 2.1. поверхности А, В, Е ) выполняют в
следующем порядке.
Во-первых, на чертеже детали находят основную
конструкторскую базу (для плоских поверхностей). Основная
конструкторская база — это поверхность, которая определяет
положение детали в сборочной единице. Признаки основной
конструкторской базы - такая поверхность на чертеже детали
координирована с другими поверхностями большим числом размерных
связей; для данной поверхности указаны более высокие требования к
точности размеров, выходящих на нее, к допускам формы и чистоте
поверхности (поверхность фланца В).
Во-вторых, определяют поверхность, которую можно
использовать в качестве черновой базы для назначения припуска на
поверхность, обозначенную конструкторской базой (см. правило выбора
черновых баз с точки зрения механической обработки [ 7 ] ). Выбор
поверхности проводят из числа поверхностей, координированных с
63
конструкторской базой размерными связями в порядке возрастания их
номинальных размеров. На выбранную поверхность ставят знак базы – V 1 .
в рассматриваемом на рис. 2.1. случае это противоположная (верхняя)
поверхность фланца В.
В-третьих, принимают в качестве базы механической обработки
конструкторскую базу (поверхность фланца В нижняя), при этом
следует поставить знак второй базы V II .
___________________________________________________
* ) В учебнике [ 1 ] параметры отливки определяются по ГОСТ 26645-85.
Рис. 2.1. Выбор баз механической обработки на чертеже детали:
А, В, С, D, E – обрабатываемые поверхности (на фланце
обрабатывается верхняя и нижняя поверхности); Ст – стержень; ВБ –
встречный болван
Затем, проверяют, все ли поверхности можно обработать
64
относительно найденных баз. Если имеется поверхность, которую нельзя
обработать от найденных баз, то для нее определяют базу механической
обработки из числа поверхностей, координированных с ней размерными
связями в порядке возрастания их номинальных размеров, и ставят знак
V III (в нашем случае для внутренней поверхности, координированной
размером 172 мм, выбираем в качестве третьей базы поверхность Е,
которая обозначается знаком V III ).
Аналогично находят черновую базу V IBP для обработки
поверхностей вращения, в том числе являющихся конструкторскими
базами (на рис. 2.1. поверхность С). Второй базой для обработки
поверхностей вращения с другой стороны (а это поверхность D) будет
поверхность С - обозначается V IIBP .
Таким образом, формируется следующая концепция обработки с
учетом принципов базирования [ 7 ]:
1) заготовка устанавливается на первый комплект баз (черновых - V 1 и
V IBP ) для токарной обработки – подрезаются торцы, обтачиваются и
растачиваются поверхности вращения, подготавливается комплект
чистовых баз для последующей обработки;
2) заготовка переставляется на второй комплект баз (чистовых - V II и
V IIBP ) для токарной обработки – подрезаются торцы, обтачиваются и
растачиваются поверхности вращения с другой стороны;
3) заготовка устанавливается на основные конструкторские базы для
обработки крепежных отверстий (сверление, нарезание резьбы),
вспомогательных конструкторских баз, функциональных и, при
необходимости, свободных поверхностей (точение, фрезерование,
сверление, зенкерование, развертывание, протягивание, шлифование и
т.д.) .
2. Определение допусков и припусков на механическую обработку
После выбора плоскости разъема и решения вопроса о
формировании внутренних и внешних поверхностей необходимо
выполнить определение допусков и припусков на механическую
обработку по ГОСТ Р 53464–2009. Ниже на примере детали ступицы
заднего колеса автомобиля марки ЗИЛ-130 (рис. 2.2, а) приведен
расчет допусков и припусков на обработку. Исходные данные:
материал - КЧ35-10, наибольший габаритный размер 326 мм, масса
22 кг, сложность отливки - средняя, термическая обработка –
графитизирующий отжиг, способ литья - в сырые песчано-глинистые
формы из смеси с влажностью 3,5-4,5%, прочностью 0,06...0,12 Н/мм 2
65
и твердостью не ниже 70 ед. Уровень механизации – машинное
поточно-механизированное производство, культура производства –
средняя. Технический уровень технологии механической обработки по
ГОСТ Р 53464–2009 - средний.
Рис. 2.2. Чертеж детали (а) и отливки (б) ступицы заднего колеса:
А, В, С, D, E – обрабатываемые поверхности (на фланце
обрабатывается верхняя и нижняя поверхности), МФ – разъем модели и
формы
66
Назначение параметров точности отливки и соответствующих им
допусков и припусков следует проводить в следующем порядке.
1. По ГОСТ Р 53464–2009 (см. в стандарте прил., табл. А.1) для
заданного технологического процесса, габаритного размера 326 мм и
сплава КЧ35-10, подвергаемого термической обработке, находим
интервал классов точности размеров КР 9— 13. Согласно примечанию,
принимаем КР 11.
2. По тому же ГОСТ Р 53464–2009 (см. в стандарте прил., табл. Б.1)
находим степень коробления элементов отливки: фланца (рис. 2.3) и
основной цилиндрической части отливки (f— стрела прогиба).
При этом при определении степени коробления фланца, точнее
его свисающих концов, за высоту принимаем толщину h = 27 мм, за
длину L — разность диаметров L = D – D 1 = 326 - 186 = 140 мм. Исходя
из отношения h / L = 0,19 с учетом разовой формы и термической
обработки отливки, интервал степени коробления составляет 5-8. В
соответствии с примечанием к таблице стандарта принимаем СКэ 7.
Следует заметить, что при определении наибольшей длины
коробящего элемента для кронштейнов, фланцев и т.п. берут удвоенную
длину концов, как, например, для ступицы фланца. При определении
степени коробления внутреннего цилиндра (рис. 2.4) за высоту
принимается диаметр D = 166 мм, за длину – L = 230мм. Тогда по
отношению D/L = 0,72 с учетом разовой формы и термической обработки
отливки попадаем в интервал стандарта 4 -7. В соответствии с
примечанием принимаем СКэ 6.
Рис. 2.3. Коробление фланца
отливки:
D, D1 – диаметры ступицы; h –
толщина фланца; f – стрела
прогиба
Рис. 2.4. Коробление цилиндра
отливки:
f – стрела прогиба; L, D, d –
высота, наружный и внутренний
диаметры ступицы
67
Степень коробления отливки в целом принимается по наибольшему
значению степени коробления элемента отливки, для нашего случая это
СК 7.
3. По ГОСТ Р 53464–2009 (см, в стандарте прил., табл. В.1) для
заданного технологического процесса, габаритного размера 326 мм и
материала КЧ35-10 (предусмотрена термическая обработка) находим
интервал степеней точности поверхности 13— 19. С учетом примечания
принимаем СП 15.
4. По тому же ГОСТ Р 53464–2009 (см. в стандарте прил., табл.
Д.1) для заданного технологического процесса, номинальной массы 22
кг и материала КЧ35-10 (предусмотрена термическая обработка)
находим интервал классов точности массы, равный 8—15. С учетом
примечания принимаем КМ 11.
5. Допуск смещения отливки определяем для наименьшей
толщины стенки в плоскости разъема по классу точности размеров
отливки, т. е. КР 11. В нашем случае h = 14 мм; по табл. 1 из ГОСТ Р
53464–2009 для КР 11 и h = 14 мм находим Т СМ = 2,8 мм.
Таким образом, найдены основные параметры точности отливки
ступицы заднего колеса: класс точности размеров КР 11, степень
коробления СК 7, степень точности поверхности СП 15, точность
массы КМ 11 и допуск смещения Т СМ =2,8 мм. В соответствии с ГОСТ Р
53464–2009 необходима соответствующая запись в ТУ отливки. Для
нашего случая записываем:
Точность отливки: 11-7-15-11 См.2,8 мм, ГОСТ Р
53464–2009.
6. Для обрабатываемых поверхностей необходимо определить ряд
припуска РП. По табл. 19 находим для степени точности поверхности СП
15 интервал ряда припусков 6 — 9. С учетом примечания принимаем РП
8.
7. Определение припусков ведем для шести обрабатываемых
поверхностей: А, В (на фланце обрабатывается верхняя и нижняя
поверхности), С, D, E, заполняя при этом последовательно табл. 26.
При определении припусков на обработку следует иметь в виду
следующее. В соответствии с ГОСТ Р 53464–2009 точность размеров,
пересекающих и выходящих на плоскость разъема, отражается в общей
надписи на чертеже отливки. Этому виду размеров присвоено
обозначение ВР2 (В — вид, Р — размер), что означает их
принадлежность к размерам, образованным двумя частями формы.
Точность размеров, образованных одной частью формы или
стержнем (обозначение ВР1), на один-два класса по ГОСТ Р 53464–2009
68
точнее размеров ВР2, а точность размеров, образованных тремя и более
частями формы, несколькими стержнями или подвижными элементами
формы, а также точность толщин стенок — на один-два класса «грубее»,
чем точность размеров ВР2.
Поэтому при назначении припусков на механическую обработку
важно знать, какими частями формы формируются внутренние и
внешние поверхности отливки (формой, болваном, стержнем). Общий
припуск назначают по табл. 26. для устранения погрешностей
размеров, формы и расположения, неровностностей и дефектов
обрабатываемой поверхности, формирующихся при изготовлении
отливки и последовательных переходах ее обработки.
Следует отметить, что величина общего допуска при нахождении
припуска зависит от схемы механической обработки. Выбор вида
механической обработки ведется по табл. 26.
Допуски размеров детали берутся с ее чертежа. Общие допуски, как
правило, назначаются по 14 квалитету, а, например, для автомобильной
отрасли и приборостроения — по 12 квалитету. После назначения
припусков на обработку в соответствии с ГОСТ 3.1125 —88 «Правила
графического выполнения элементов литейной формы и отливок» с
учетом чертежа детали разрабатывается чертеж отливки или на чертеж
детали наносятся найденные значение припусков. Отверстия, которые
«не проливаются» (т.е. не могут быть изготовлены в процессе получения
отливки), необходимо «заглушить» (показано на рис. 2.2, б).
Кроме припусков на механическую обработку на чертеж детали
наносят плоскость разъема, формовочные уклоны (сверх припусков для
обрабатываемых поверхностей), литейные радиусы и радиусы
сопряжения толщин стенок.
Контуры отливки обводят жирными линиями, тогда как контуры
детали показаны тонкими линиями (см. рис. 2.2, б). На чертеже отливки
(или чертеже детали с нанесенными размерами отливки) следует
указывать измерительные базы (базы разметки) и базы первоначальной
обработки поверхностей.
Допуски проставляются только на линейные размеры отливки,
отличающиеся от указанных общей надписью. Текст технических
условий на отливки формируется с использованием технических
условий чертежа детали. После нанесения припусков при необходимости
проводится окончательная проверка проливаемости отверстий и
формуемости болванов.
69
Таблица 26. Определение общих припусков
на механическую обработку поверхностей отливки «ступица»
Параметр Значение параметра для обрабатываемой
поверхности
А В С D Е
Номинальный размер N H от базы
до обрабатываемой поверхности,
мм
158 27 99 135 150
Вид размера ВР 2 2 2 1 1
Класс точности размеров КР 11 11 11 10 10
Допуск размера отливки Т 0 5,0 3,6 4,4 3,2 3,2
Номинальный размер* 1
нормируемого участка № н ,. у
обрабатываемой поверхности
166 160 170 79 69
Номинальный размер
нормируемого участка базовой N б н.у
поверхности* 1
156 156 160 27 27
Степень коробления отливки СК 7 7 7 7 7
Допуск формы и
расположения поверхностей
отливки Т о.ф
0,8 0,64 0,8 0,5 0,5
Допуск формы и расположения
базовой поверхности отливки Т ф.баз
0,64 0,64 0,64 0,5 0,5
Допуск смещения Т см — — —. 2,8 2,8
Номинальный размер N D
диаметра фланца D
— — — 326 326
Вид размера ВР — — — 1 1
Клacc точности размеров КР — — — 10 10
Допуск Т D номинального размера
D
— — — 4,0 4,0
Допуск позиционный Т поз = Т D /2 — — — 2,0 2,0
Общий допуск T о.общ * 2 5,0 4,0 5,0 6,4 6,4
Механическая обработка а в а б б
Общий допуск при
назначении припуска
5,0 2,0 5,0 3,2 3,2
Общий припуск на обработку
Z общ
3,8
5,3
6,0
6,7
2,2
3,0
3,4
3,6
3,8
5,3
6,0
6,7
2,9
4,0
4,5
4,8
2,9
4,0
4,5
4,8
Вид механической обработки
Черновая Тонкая
__________
*1 При определении припуска необходимо учесть тот факт, что
коробится не только обрабатываемая, но и базовая поверхность,
70
относительно которой происходит обработка. Номинальным размером
нормируемого участка поверхности N о н.у является поверхность, на
которой происходит коробление или которая обрабатывается.
Номинальным размером нормируемого участка базовой поверхности
N б н.у является поверхность, на которой происходит базирование.
*2 См. в ГОСТ Р 53464–2009.
2.5.2. Пример 2 - корпусная деталь. «Корпус редуктора»
Исходные данные: отливка – серый чугун, серийное производство,
наибольший габаритный размер отливки – 325 мм (номинальный
размер + 0,5 припуска), толщина стенки 12 мм, высота отливки 320 мм,
сложность отливки – средняя (рис.2.5).
1. Определение точности отливки
Отливка изготавливается в песчано-глинистых формах из
высокопрочных смесей с влажностью от 2,2% до 3,5% и средним
уровнем уплотнения до твердости 80 единиц. Диапазон класса точности
(табл.11) – от 8 до 13т. Для отливок из серого чугуна средней
сложности в условиях механизированного серийного производства
назначаем 11 класс размерной точности отливки.
Для указанного вида литья при массе отливки от 10 до 100 кг
диапазон класса точности массы по табл. 12 от 11 до 18. С учетом
дополнительных условий, указанных выше, назначаем 12 класс
точности массы отливки.
Для данного вида литья диапазон степени точности поверхности с
наибольшим габаритным размером от 250 до 630 мм (табл. 15)
составляет от 11 до 18 степени. С учетом дополнительных условий,
указанных выше, назначаем 15 степень точности поверхности. Допуск
неровностей поверхности для 15 степени точности (табл. 13) составляет
1,2 мм, что соответствует значению шероховатости Ra 50 мкм (табл.
14).
Степень коробления элементов отливки определяется на
основании отношения наименьшего размера элемента отливки к
наибольшему. Для данной отливки наименьшее отношение (толщины
стенки отливки (12 мм) к ее высоте (320 мм)) составляет 0,03. По табл.
17 диапазон степени коробления отливок необрабатываемых
термически и получаемых в разовых формах, составляет от 6 до 9. Для
отливки средней сложности устанавливаем 8 степень коробления.
71
Допуски формы и расположения отдельных элементов отливки
назначаем по табл. 16 по номинальному размеру нормируемого участка.
Определение допуска смещения по плоскости разъема по табл. 18
для данного класса размерной точности отливки по наименьшему
номинальному размеру элемента отливки, выходящему на разъем
литейной формы. В данной отливке таким элементом является стенка
корпуса толщиной 12 мм. Допуск смещения отливки – не более 2,8 мм.
Таким образом, условное обозначение точности отливки корпуса
редуктора может быть указано следующим образом: точность
отливки 11–8–15–12 см. 2,8 ГОСТ Р 53464–2009.
2. Определение припусков на обрабатываемые поверхности
Диапазон ряда припусков на обработку устанавливают по табл. 19.
Для 15–й степени точности поверхности отливки из серого чугуна
принимаем 6-й ряд припусков.
В данном примере определяем припуски на 3 поверхности (см. рис.):
- плоскость основания – поверхность А;
- торцевые поверхности бобышек основного отверстия –
поверхности В и Г;
- нижнее отверстие – поверхность Б.
А) Плоскость основания (поверхность А)
Требования к точности плоскости основания детали:
Допуск размера – 1,4 мм;
Допуск плоскостности – 0,1 мм;
Шероховатость поверхности Rz 25 (Ra6,3).
Точность плоскости основания отливки:
Допуск размера данного элемента (320 мм) по табл.18 для 10
класса размерной точности составляет 4 мм, при симметричном
расположении допуска ±2,0 мм.
Допуск на данный размер устанавливаем на 1 класс точнее (т.е. 10-й),
чем класс размерной точности отливки (11-й), так как он (допуск)
обеспечивается одной частью литейной формы.
Допуск формы и расположения данной поверхности отливки не
указан, поэтому он принимается равным 25% допуска
соответствующего размера отливки, т.е. 1,0 мм. По табл.21 отношение
допуска размера обрабатываемой поверхности детали (1,4 мм) к
соответствующему допуску размера отливки (4 мм) составляет 0,35 мм,
72
что требует двух этапов обработки: черновой и получистовой. По табл.
22 отношение допуска формы и расположения обработанной
поверхности детали (0,1 мм) к соответствующему допуску отливки (1
мм) составляет величину 0,1. В соответствии с данными табл. 22 в
технологическом процессе следует принять три этапа обработки:
черновую, получистовую и чистовую.
Общий допуск размера, формы и расположения обрабатываемой
поверхности определяем в соответствии с табл. 23. При допуске
размера 1,4 мм и допуске формы и расположения обрабатываемой
поверхности 0,1 мм принимаем общий допуск равным 1,6 мм.
В соответствии с табл. 25 следует оценить уровень точности
металлорежущего оборудования, применяемого в технологическом
процессе. При использовании станков с ручным управлением следует
оценить уровень точности, как пониженную и при определении общего
припуска использовать интервала общего допуска в табл. 24 на 1 строку
ниже, т.е. вместо интервала св.1,4 до 1,6 мм назначить припуск из
интервала св.1,6 до 1,8 мм.
По табл. 2.14 для трех этапов обработки и 6-го ряда припусков
принимаем общий припуск на обрабатываемую поверхность плоскости
основания 2,6 мм, из них 1,7 мм на черновую обработку, 0,6 мм – на
получистовую и 0,3 мм – на чистовую.
Б) Торцевые поверхности бобышек (поверхности В и Г)
Требования к точности плоских поверхностей бобышек:
Допуск размера – 0,4 мм;
Допуск формы и расположения – не заданы;
Шероховатость поверхности Rz 25 мкм (Ra 6,3).
Определяем точность поверхностей торцов бобышек отливки
Допуск данного элемента (размером 160 мм) по табл. 2.8
составляет 3,2 мм (для 10 класса размерной точности, т.к. оба торца
отливаются в одной части формы). По таблице 19 устанавливаем 6-й
ряд припусков.
Допуск формы и расположения торцевой поверхности детали не
указан, принимаем его в пределах допуска на размер – 0,4 мм. Допуск
формы и расположения торцевых поверхностей отливки не указан.
Принимаем его равным 25% допуска на размер – 0,7 мм. Отношение
допуска на размер детали (0,4 мм) к допуску на размер отливки (2,8
мм) составляет 0,13, что требует (табл. 21) трех этапов обработки:
черновой, получистовой и чистовой. Отношение допуска формы и
73
расположения поверхностей детали (0,4 мм) к соответствующему
допуску отливки (0,7 мм) составляет 0,6. в соответствии с табл.22 для
обработки достаточно одного этапа. Принимаем данные табл.21:
черновой, получистовой и чистовой этапы обработки.
Общий допуск размера, формы и расположения обрабатываемых
поверхностей определяем в соответствии с табл.23. При допуске
размера 0,4 мм и допуске формы и расположения обрабатываемой
поверхности 0,4 мм общий допуск обрабатываемого элемента
составляет 0,64 мм. По таблице 25 оцениваем уровень точности
применяемого оборудования, как пониженный и понижаем интервал
общего допуска на одну строку (табл. 24). Общие припуски на
противоположные поверхности, используемые в качестве взаимных
баз при обработке, назначают по половинным значениям общих
допусков отливки (см. пункт 4.2.1 ГОСТ Р 53464–2009) [5], поэтому
принимаем в расчет общий допуск 0,64/2 = 0,32 и по табл.24 для
интервала св. 0,32 до 0,4 мм определяем общий припуск на сторону
2,7 мм: на черновую обработку – 2,3 мм; на получистовую обработку –
0,3 мм; на чистовую обработку – 0,2 мм.
3.Основное отверстие (поверхность Б)
Требования к точности отверстия:
Допуск диаметра – Ø80 Н8 (+0,046);
Точность формы – в пределах допуска на размер;
Точность расположения – 0,2 мм;
Шероховатость – Rа 1,6 мкм.
Точность диаметрального размера отливки 4,4 мм. Степень
точности поверхности – 15-я. Точность расположения оси отливки –
2,0 мм (табл. 16).
Отношение допуска на размер детали (0,046) к допуску на размер
заготовки (4,4 мм) равно 0,01. в соответствии с таблицей 21 в
технологии необходимо использовать все четыре предусмотренных
ГОСТом этапа механической обработки: черновую, получистовую,
чистовую и тонкую. Так как в соответствии с табл.21 требуется
использовать максимальное число этапов обработки для обеспечения
требуемой точности размеров данного элемента детали, то проверку
необходимого числа этапов для обеспечения требуемого повышения
точности формы и расположения поверхностей можно не проводить.
Обработку отверстия предполагается проводить на станках
повышенной точности, оснащенных устройством ЧПУ, поэтому
уровень точности применяемого оборудования принимаем
74
повышенный (табл.25) и повышаем интервал общего допуска для
определения припуска на одну строку в табл.24.
Механическую обработку отверстия предполагается проводить
от технологической базы – плоскости основания, допуск размера от
которой до оси обрабатываемого отверстия равен 0,2 мм. Допуск
формы отверстия ограничен допуском размера (0,046 мм). В
соответствии с табл.23 общий допуск на обрабатываемое отверстие
составляет 0,22 мм.
2 5 0
1 6 0 - 0 , 4
1 4 0
1 2 + 0 , 4 3
2 0 5
R a 1 , 6
 Ã
R a 2 5
R a 2 5
R a 2 5
Á
À
0 , 1
Рис. 2.5. Корпус редуктора (пример для расчета припусков на
поверхности А, Б, В и Г)
75
Библиографический список
Основной
1. Технология литейного производства: Литье в песчаные
формы: Учебник для студ. высш. учеб. заведений /
А.П.Трухов, Ю.А. Сорокин, М.Ю. Ершов и др.; под ред. А.П.
Трухова. – М.: Издательский центр «Академия», 2005. – 528
с.
2. Салтыков В. А. Технология машиностроения. Технология
заготовительного производства : учеб. пособие / В. А.
Салтыков, Ю. М. Аносов, В. К. Федюкин. СПб : изд-во
Михайлова В. А., 2004. 336 с.
3. Руденко П. А. Проектирование и производство заготовок в
машиностроении : учеб. пособие / Руденко П. А., Харламов
Ю. А., В.М. Плескач, под общ. ред. В.М. Плескача. К.:
Наукова думка, 1991. - 247 с.
4. Расчет припусков и межоперационных размеров в
машиностроении : Учеб. пособие / Х. М. Радцевич и др. ; под
общ. ред. В. А. Тимирязева. М.: Высшая школа, 2004. 272 с.
5. Машиностроение : энциклопедия. В 40 т. М.:
Машиностроение, 1999. Т.III -2. 840 с.
6. ГОСТ Р 53464–2009. Отливки из металлов и сплавов.
Допуски размеров, массы и припуски на механическую
обработку. М.: Изд-во стандартов, 2009. 54 с.
7. Справочник технолога–машиностроителя / под ред. А. Г.
Косиловой и Р. К. Мещярекова. В 2 т. М.: Машиностроение,
1986. Т.1. 655 с.
8. Технология конструкционных материалов : метод. указания
к выполнению курсовой работы по разделу «Литейное
производство» / сост.: В. И. Черменский, и др. Екатеринбург :
УГТУ – УПИ, 2000. 32 с.
9. ГОСТ 3.1125 – 88. Конструирование литых заготовок. М.:
Изд-во стандартов, 1988. 31 с.
10. ГОСТ 3212 – 92. Формовочные уклоны. М.: Изд-во
стандартов. 1992. 25 с.
11. Сборник практических работ по технологии машиностроения
: учеб. пособие / А. И. Медведев и др.; ред. И. П. Филипова.
Минск : БнТУ, 2003. 486 с.
12. Специальные способы литья : справочник / под общ. ред. В.
А. Ефимова. М.: Машиностроение, 1991. 430 с.
76
13. В. Н. Иванов. Специальные виды литья : учеб. пособие / В. Н.
Иванов, М.: МГИУ, 2007. 316 с.
14. М.Г. Афонькин, В.Б. Звягин. Производство заготовок в
машиностроении. СПб.: Политехника, 2007. 380 с.
15. Выбор заготовок в машиностроении: уч. пособ. / А.С.
Васильев, А.И. Кондаков. М.: МГИУ, 2002. 80 с.
16. Сорокин Ю.А., Максимов А.Д. Технологическая модель и
алгоритм назначения баз механической обработки для САПР
чертежа отливки // Литейное производство, 1998, №4. С. 36.
Дополнительный
17. Технология литейного производства. Учебник / Чуркин Б.С.,
Гофман Э.Б., Майзель С.Г., Афонаскин А.В., Миляев В.М и
др. Под редакцией Б.С.Чуркина. Екатеринбург: Изд-во Урал.
Гос. Проф. – пед. Ун-та, 2000. 652 с.
18. Производство заготовок в машиностроении. / М.Г.
Афонькин, М.В. Магницкая Л.: Машиностроение, 1987. 352
с.
19. ГОСТ 3212–92 стержневые знаки. Основные размеры. М:
Изд-во стандартов. 1980. 24 с.
20. Литые заготовки и способы их получения. / Филлипов Г.И. Л:
Машиностроение, 1985. 86 с.
21. Кокильное литье: Справочное пособие./ Дубинин Н.П.,
Беликов О.А., Вязков А.Ф. М.: Машиностроение, 1967. 460 с.
22. Литье по выплавляемым моделям / под ред. Н.И. Шкленника,
В.А. Озерова. М.: Машиностроение, 1971. 456 с.
23. Коротков А И., Полевая А.М. Литье в оболочковые формы.
М.: Машгиз, 1963. 360 с.
24. Юдин С.Б., Розенфельд С.Е., Левин М.М. Центробежное
литье. – М.: Машиностроение, 1972. – 360 с.
25. Литье под давлением / А.К. Белопухов, В.И. Винберг, А.А.
Дудин и др. М.: Машиностроение, 1975. 400 с.
26. Специальные способы литья / Под ред. Е.Б. Гуляева, А.М.
Липницкого, Ф.Д. Оболенцова. Л.: Машиностроение, 1971.
286 с.
27. ОСТ 23.4.50 – 73., ОСТ 23.1.51.73 Отливки из алюминиевых
сплавов. М.: Минсельхозмашиностроение, 1981. 47 с.
28. Воробьев Ю.А. Точность деталей, получаемых литьем и
прессованием из цветных сплавов и пластмасс. М.:
Машиностроение, 1963. 175 с.
29. Василевский П.Ф. Технология стального литья. М.:
77
Машиностроение, 1974. 402 с.
30. Скарбинский М. Конструирование отливок. М. – Л.: Машгиз,
1961. 574 с.
31. Справочник по чугунному литью / Под. Ред. Н.Г. Гиршовича.
Л.: Машиностроение, 1978 758 с
32. Рихтер Р.А. Конструирование технологичных отливок. М.:
Машиностроение, 1968. 254 с.
33. Технологические основы обеспечения качества машин / под
общ. ред. К.С. Колесникова, М.: Машиностроение,1990.256 с.